Working smarter, cleaner and greener: The future of manufacturing and materials
31/05/2023
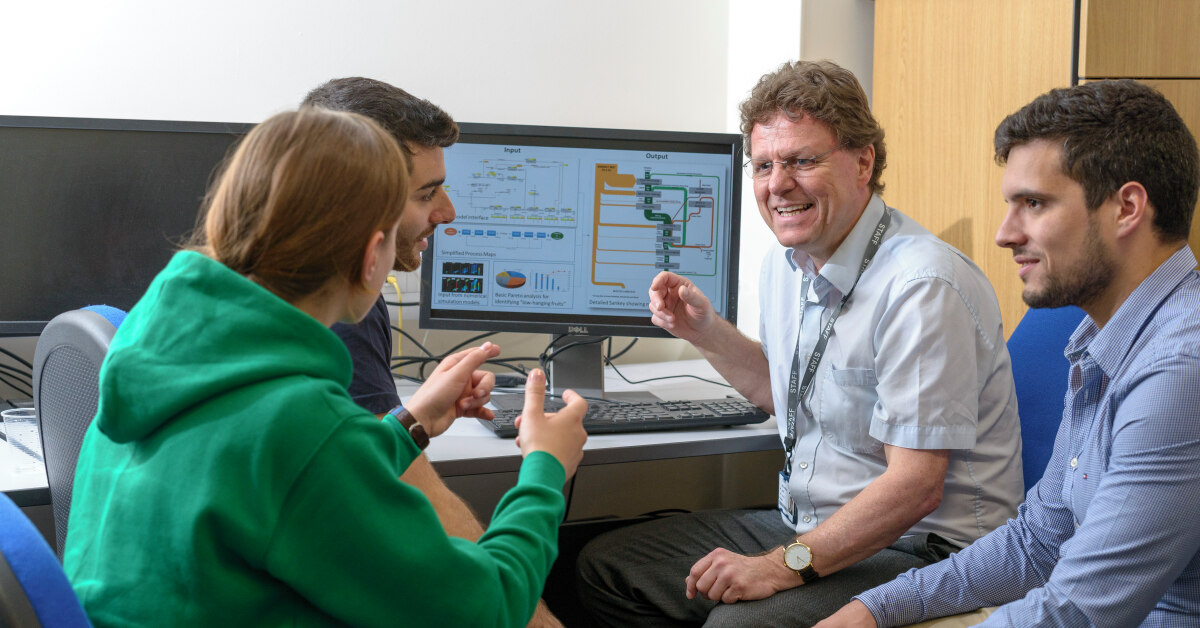
Everything we own, use or interact with in life starts with a material or materials. But even we in the industry admit that materials are a huge part of what has led us to where we are today – i.e., facing a global climate crisis of terrifying magnitude.
As humans, we have dug so much out of the ground, used a lot of energy in converting those materials into items for use or consumption, and then sold them – often according to the ‘pile it high, sell it cheap’ philosophy.
Collectively, our sector has a responsibility to do better. At Cranfield University, we’re trying to reverse the tide.
Our MSc courses – including our Advanced Materials MSc, Digital and Technology Solutions MSc and dedicated Aerospace Materials MSc – are instructing, enabling and encouraging the next generation of manufacturing and materials professionals in pursuing a future that is smart, clean and green. We’re also working with partners in industry to help solve the challenges facing the sector according to the same ethos.
More than 70 countries worldwide, including the UK, have pledged to reach net zero by 2050 – a target we must meet, or face the consequences.
At Cranfield, we believe in thinking holistically in pursuit of a more sustainable manufacturing and materials sector, and so our research – and subsequent teaching – spans the triumvirate of resource efficiency, process efficiency and operations efficiency.
Because new technologies and innovations alone will not get us where we need to be. To stand any chance of reaching net zero, we must reduce our consumption of materials by 50%. But how can we do that when all our business models revolve around that consumption? We need policy change, social change and philosophical change. The challenge is huge.
“Transitioning to a net zero world is one of the greatest challenges humankind has faced. It calls for nothing less than a complete transformation of how we produce, consume, and move about.” United Nations
In the early 1700s, Abraham Darby I invented the blast furnace to fulfil demand for his patented cast iron cooking pot. The pig iron he made in that blast furnace was then taken by Henry Bessemer in the mid-1800s and turned into steel in a process that involved using oxygen in air blown through the molten pig iron to burn off the large amount of carbon (around 4%) introduced by the Darby blast furnace process, creating huge volumes of CO2 in the process.
We are still using those technologies today. We’re putting carbon in to make pig iron and taking it out again to make steel, instead of making steel by a different process that is cleaner, greener and uses fewer materials – which has been and can be done.
As Director of UK Research and Innovation’s TransFIRe project, I am involved in discussions about how we can infl uence policy and get the message across that we need to make and use less, as well as better value those materials already in use by reusing them, repurposing them, and making them last longer.
We believe there is an urgent need for new thinking in the sector.
We’ve created a whole industry based on and managed in using old technology, and we’re still using the same technology and the same thinking to run it – and expecting different results.
We need to change the technology, change the team, and change the tactics. At Cranfield, we’re an international community.
Our leading thinkers and innovators seek to break down barriers, embracing difference of experience and thinking in pursuit of enhanced creativity and innovation.
When you have a problem to solve, it’s no good bringing together a group of people with the same skills and experience. Unlocking creativity comes from blending together a mixture of people who bring different perspectives.
We need to be less bound by our history and embrace and encourage diversity of thinking. Only then do we stand a real chance of getting to where we need to be – manufacturing smarter, cleaner and greener.
Towards net zero
Some of the sustainable manufacturing and materials work currently underway at Cranfield includes:
- Working with National Grid to turn methane into a paint technology that can be used to coat hydrogen gas pipes to prevent leaks.
- Working with medical suppliers to develop reinforced surgical gloves made from natural rubber that are quicker and require less energy to manufacture, are better in use, and are made from sustainable materials.
- Exploring the capabilities of Wire Arc Additive Manufacturing to use fewer materials and less energy in a process that is more cost effective.
About the author:
Professor Mark Jolly currently leads the manufacturing capabilities at the University. He is Professor of Sustainable Manufacturing and Head of the Sustainable Manufacturing Systems Centre. He is also Co-director of the EPSRC Centre for Doctoral Training in Sustainable Materials & Manufacturing, run in collaboration with the Universities of Warwick and Exeter.
Mark has a Bachelor of Metallurgy degree from Sheffield University and a PhD in metallurgy from Cambridge University.
Categories & Tags:
Leave a comment on this post:
You might also like…
Meet Mendeley: a powerful referencing tool that does the hard work for you!
Are you looking for a way to manage your references, create in-text citations and reference lists for your assignments or thesis? If so, you may wish to consider using Mendeley. What is it? Mendeley is ...
Adding documents to your Mendeley account
To make the most of a Mendeley account, it is useful to create and maintain a ‘Library’ of references. You can add references and documents to this Library in a number of ways: 1) Drag ...
Choosing the right reference management tool for you…
Are you thinking about using reference management software to help you manage your references? The Library is here to help you. While Mendeley has been our go-to reference management software for some years, we've recently ...
Cranfield Seed Fund recipient, Cosysense, are using AI to solve air conditioning problems and provide a net zero alternative
If you’ve ever worked in an office environment you’ve probably been involved in, or overheard, a conversation about the air conditioning. Well, it’s no surprise it’s a common complaint when research shows that up ...
An Eye-Opening Journey in Advanced GIS & Remote Sensing at Cranfield University
My experience in the Advanced GIS and Remote Sensing course at Cranfield University was nothing short of transformational. From day one, the course was designed to provide both technical expertise and real-world applications. What ...
EBSCO databases – User interface changes
EBSCO has recently introduced a new user interface which you will see when you access any of our EBSCO databases - Business Source Complete, EBSCO eJournals and eBooks, GreenFILE, PsycARTICLES and PsycINFO. If you've used ...