The Fresh Connection Global Challenge
22/04/2021
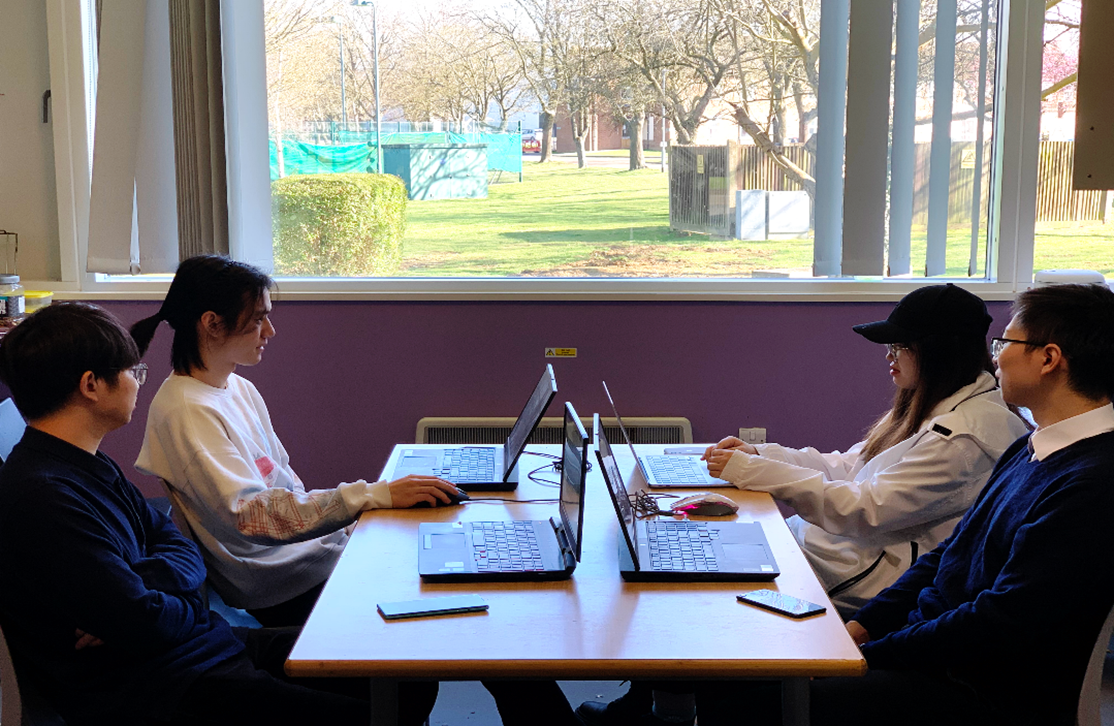
The Fresh Connection Global Challenge (TFC), part of the syllabus for Logistics and Supply Chain Management MSc and Procurement and Supply Chain Management MSc, is a very enjoyable and educational simulation for us. After solving different challenges and dealing with different scenarios as part of the simulation, we have practiced what we have learned from course modules like, Safety Stock in Inventory and Operations Management, to gain a better understanding of the supply chain.
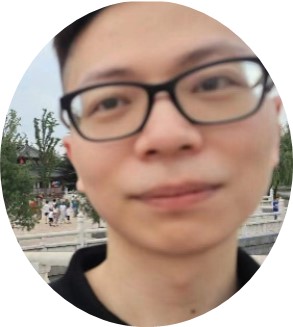
My role in TFC was Supply Chain Manager. I was responsible for communicating and collaborating with three other departments to maintain stability in the supply chain, including stock safety and performance improvement. In the beginning, our financial performance did not meet our expectations due to several issues with our suppliers. Even when we had selected a secondary supplier to help, we experienced a break in the supply chain which resulted in a significant loss. After a discussion with our teammates, we decided to adopt an agile strategy to improve our income, which was effective. Meanwhile, a lean strategy was also taken into consideration in several operational parts to reduce the emission of CO². Overall, TFC helped me understand how to implement supply chains and improved my understanding of different kinds of strategies by working through real life examples and challenges to find solutions.
—Xuanhong Wan
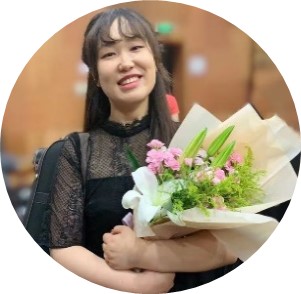
My role in TFC was Purchasing Manager. I was responsible for controlling procurement costs, coping with external risks and cooperating with operations, sales and supply chain control departments to meet customer needs and maximize returns. I found that purchasing is one of the most important departments in a company, as they are required to negotiate with suppliers, while maintaining good relationships with them, and find the most cost-effective solutions to buy materials. It is impossible to get the job done without cooperation. I discussed the purchasing decisions with my teammates. To achieve the best grade possible, we concluded that it was best not concern ourselves with the individual performance of the departments but look at the company as whole for example, I selected suppliers with higher prices but better quality for the stability of the whole supply chain and sacrificed cost savings, which is a key indicator for the purchasing team’s success. Fortunately, we got good results in the competition. It’s been a great honour to work with my teammates, I learnt a lot from them. I hope we can do even better in the final round of the competition.
—Yiran Xin
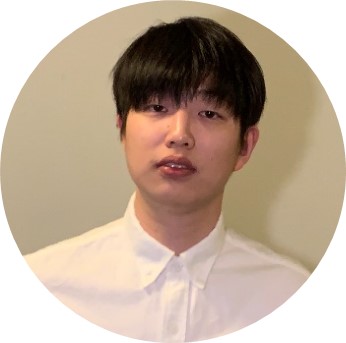
TFC is a splendid opportunity to manage the business routine. In this simulation, I played the role of Operations Manager, handling the machine types, number of workers, warehouse capability, and new technology introduction. The previous experience of simulation in Supply Chain Strategy and Sustainability (SCSS) classes helped us a lot. I realised that every department should not simply pursue their own goals, such as high warehouse utilisation rate or low fabrication cost, and the most important goals of corporate profit and sustainability. During the simulation, we cooperated with each other and collectively discussed and decided every variable. I am excited to participate in the final round with these teammates.
—Yihang Xiong
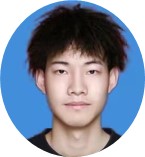
TFC really provided me with a fantastic experience. I played the role of Marketing Manager in the simulation, organising contracts with three major customers and doing market forecasting. The feeling of fighting for the same goal in a group was both exciting and rewarding. I was impressed by the well-designed system and the way the technology was used to bring the best outcomes. This simulation also gave me great insight into the structure of companies’ internal departments and the trade-offs/interactions between them. Initially we had some big ambitions to make huge cost savings and much more higher contract prices, but once we rationalised this, we came to the conclusion that the best way forward would actually be to make a few simple changes to the system to avoid unaffordable risks, followed by steps to gradually make improvements over time.
—Hongyu Zhang
Categories & Tags:
Leave a comment on this post:
You might also like…
Credibility, confidence and collaborative focus: The impact of studying for a sustainability apprenticeship at Cranfield
For participants on Cranfield’s Sustainability Business Specialist Apprenticeship, it doesn’t take long for their studies to start to have an impact, with that impact ranging from personal growth and career progression, to organisational effect ...
Meet Mendeley: a powerful referencing tool that does the hard work for you!
Are you looking for a way to manage your references, create in-text citations and reference lists for your assignments or thesis? If so, you may wish to consider using Mendeley. What is it? Mendeley is ...
Adding documents to your Mendeley account
To make the most of a Mendeley account, it is useful to create and maintain a ‘Library’ of references. You can add references and documents to this Library in a number of ways: 1) Drag ...
Choosing the right reference management tool for you…
Are you thinking about using reference management software to help you manage your references? The Library is here to help you. While Mendeley has been our go-to reference management software for some years, we've recently ...
Cranfield Seed Fund recipient, Cosysense, are using AI to solve air conditioning problems and provide a net zero alternative
If you’ve ever worked in an office environment you’ve probably been involved in, or overheard, a conversation about the air conditioning. Well, it’s no surprise it’s a common complaint when research shows that up ...
An Eye-Opening Journey in Advanced GIS & Remote Sensing at Cranfield University
My experience in the Advanced GIS and Remote Sensing course at Cranfield University was nothing short of transformational. From day one, the course was designed to provide both technical expertise and real-world applications. What ...