LSCM and PSCM get an insight into large-scale warehouse operations
26/01/2018
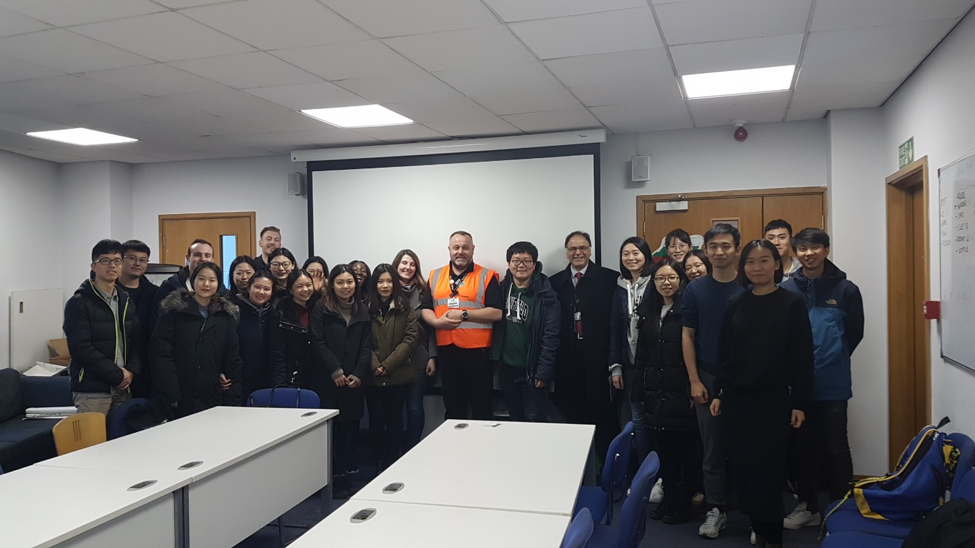
The MSc Supply Chain program at Cranfield is loaded with various activities both fun and educational in nature – such as a study tour to Europe, hosting guest speakers from the industry, an unforgettable Christmas party etc.
Activities in 2018 for the students of the MSc in Logistics and Supply Chain started on a high note, with warehouse visits being organised in cooperation with various retailers, in order to gain a better understanding and experience the inner workings of the heart of the retail industry – Distribution Centers (DCs).
Milton Keynes, with its ideal location adjacent to the primary highways of the country, and its unique setting, has encouraged the setting up of DCs for some of the biggest retailers in the UK. Companies such as Amazon, H&M, John Lewis, River Island etc, are just a few miles down the road from Cranfield University. This is why it could have not been a more ideal opportunity for this year’s supply chain students, us, to go and see some of them, making use of the close proximity.
I had the opportunity to be a part of the group who were visiting House of Fraser’s DC, which is being run by XPO Logistics, who is their Supply Chain Partner. XPO Logistics is one of the world’s ten largest providers of transportation and logistics services. The Supply Chain General Manager of XPO Logistics UK and Ireland, Mark Davies, guided us on our tour. The DC, was not running at full capacity, as we were touring at times that were earlier than their peak load schedules and he pointed out the various sections in the DC as well as the working of various equipment. House of Fraser’s DC could receive orders up to midnight, for next day delivery to all locations across the UK. The orders were released in waves and they were sent separated into totes, using a pick-to-light system that we had learned about in class. Mini load retrievers, auto-bagging machines, auto cardboard packaging machines, tilt sorters etc. were employed in the DC. It was incredible to see some of the equipment we had learnt about in classroom lectures, being actively utilised.
Apart from this, there was also a dedicated returns area. Returns are a growing concern in the retail industry today, 2.5 billion from the Christmas season alone for the industry. Well versed inspectors and a well-organized system ensured that all the returns were processed within 24 hours of entering the factory.
The entire visit lasted for little over an hour, followed by the opportunity to interact with Mark regarding any queries which was very helpful and much appreciated. It was one of the most productive learning experiences at campus, which is why we look forward to the upcoming European study tours, to gain some more industry insights.
Rahul
—
Some of us were lucky enough to be a part of the group who was going to see John Lewis’s warehouse system. Ever since it’s initial opening in 1864, the company has managed to become the UK’s largest multi-channel business. The John Lewis Partnership also includes Waitrose supermarkets as well as textiles factories and farms.
Personally, I had never seen a warehouse on this scale before, so my overall first impression of the organisation left me speechless. We were received with a warm welcome from some John Lewis team members, who gave us a brief introduction of the company’s success story, but also the challenges they were facing on a daily basis.
After this, we were split into groups, to prevent the likelihood of mingling (you don’t want that in a working warehouse) and off we went. As soon as we entered the facilities, the overall first impression led to open mouths gazing at the scale and height of a fully digitally operated product allocation systems. Such a reaction was triggered on a regular basis, throughout the visit. What really stunned me the most was the cleanliness and lack of human workforce throughout the entire warehouse. John Lewis is a renowned leader, having successfully implemented a digital warehouse system facilitating their operations and making their work more efficient. When being asked about shutdowns or system failures, it was hard to remember the last time anything major like that happened, which just reinforces the effectiveness behind their operations. This allows the company to satisfy customer demand, especially in times of distress such as Black Friday or Christmas. Having split the warehouse into different areas, according to product size, demand and structure but also online and shop orders, allows the retailer to effectively allocate goods. Products will then be picked, depending on the order and transferred over to the automated packing area. After this goods will be allocated to their final point of destination and leaving the warehouse sooner than you could ever imagine. Some items will be unpacked and dispatched again within no longer than 73 min, if it is in high demand. Fascinating!
Overall, I can say it was an honour to have had a sneak peak into one of the most efficient warehouse operation systems in the country and have learnt A LOT within that time. I have left the warehouse with excitement, fascination and inspiration in regards to what companies nowadays are capable of achieving.
Kim
Only when we as customers do not receive our orders on time, is when we start to wonder about what could have taken that long for a late delivery. Warehouses are key continuously shortening delivery times, e-retailers are promising to their customers. I had the opportunity to visit Travis Perkins, which is one of the biggest retailers of home utility, improvement and enhancement items in the UK. The warehouse we visited is one of two facilities one located in Northampton and one in Milton Keynes. This warehouse houses £80 million worth of products on average throughout the year
After a brief introduction to the company and health and safety explanation, we were guided through the massive warehouse from one stage to another and were explained the operations taking place at each stage. The warehouse stocks any product from a bathtub to bolts and everything in the middle to be fitted inside the building. We started off with the main storing area where products were placed on approximately three floors high racks. we progressed forward through a section where comparatively smaller items like screws, bolts, and fittings were kept. Then we were taken to the in-bound and out-bound area. This area consisted of three to four loading bays on each side, dedicated to out-bound and in-bound traffic. Here the team explained how the product is off loaded in the morning from inbound trucks coming from manufacturers across the country. The product is then assembled in a temporary holding area near the loading bays. Products are given unique barcodes and in-warehouse identity. During the day and until evening the products are transferred to the main storage area and are kept randomly. The crew then preps itself for another part of the operation where, according to orders received from the customers, picking task commences. Workers with forklifts and hand lifts start picking products from the shelves of the racks. These products are then brought near the loading area, palletised and then loaded onto out-bound trucks.
Something like the workings of a warehouse cannot be entirely understood until experienced and that was the exact role that the visit played. The experience was very intuitive and one of the best ways to understand why your next online order might be late.
Rohan
THANK YOU CRANFIELD UNIVERSITY AND ALL CONTRIBUTING FIRMS – WE TRULY HAD A BLAST!
—
Find out more about our Supply Chain Management programmes…
Categories & Tags:
Leave a comment on this post:
You might also like…
Credibility, confidence and collaborative focus: The impact of studying for a sustainability apprenticeship at Cranfield
For participants on Cranfield’s Sustainability Business Specialist Apprenticeship, it doesn’t take long for their studies to start to have an impact, with that impact ranging from personal growth and career progression, to organisational effect ...
Meet Mendeley: a powerful referencing tool that does the hard work for you!
Are you looking for a way to manage your references, create in-text citations and reference lists for your assignments or thesis? If so, you may wish to consider using Mendeley. What is it? Mendeley is ...
Adding documents to your Mendeley account
To make the most of a Mendeley account, it is useful to create and maintain a ‘Library’ of references. You can add references and documents to this Library in a number of ways: 1) Drag ...
Choosing the right reference management tool for you…
Are you thinking about using reference management software to help you manage your references? The Library is here to help you. While Mendeley has been our go-to reference management software for some years, we've recently ...
Cranfield Seed Fund recipient, Cosysense, are using AI to solve air conditioning problems and provide a net zero alternative
If you’ve ever worked in an office environment you’ve probably been involved in, or overheard, a conversation about the air conditioning. Well, it’s no surprise it’s a common complaint when research shows that up ...
An Eye-Opening Journey in Advanced GIS & Remote Sensing at Cranfield University
My experience in the Advanced GIS and Remote Sensing course at Cranfield University was nothing short of transformational. From day one, the course was designed to provide both technical expertise and real-world applications. What ...