Logistics and Procurement Supply Chain study tour – Vienna, day two
25/04/2017
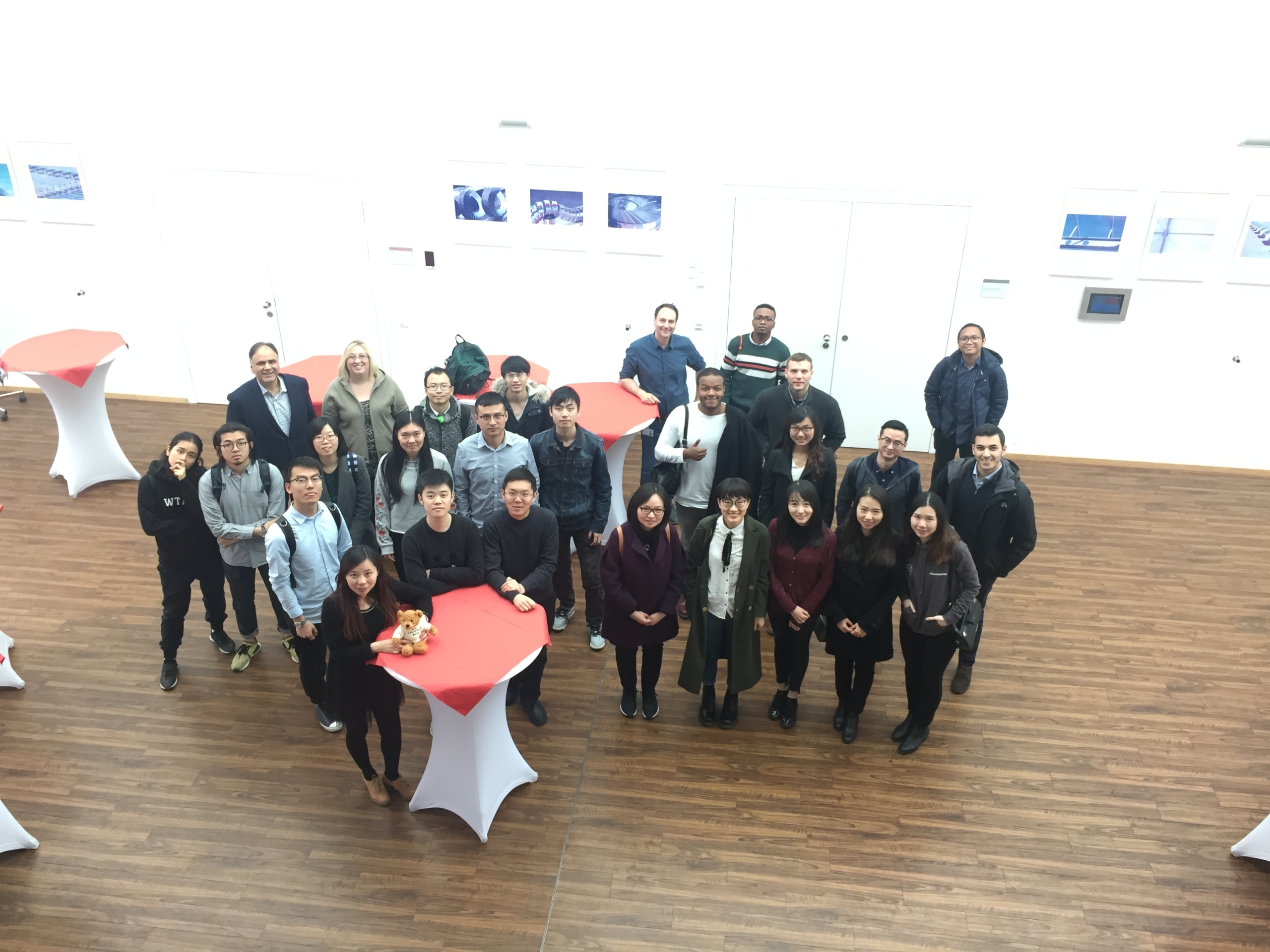
Hi everyone!
Day two of our study tour was quite exciting. We traveled to Fronius International and the BMW Engine plant.
The roads on day two were covered in snow. It’s completely white. We took the coach from the hotel to Fronius International in Sattledt. We had a short introduction to the company and a plant tour. This plant produces battery charging systems, welding systems and solar inverters. They have developed a sustainable program which is called “24 hours of sun vision”. The emphasis is on making renewable energy more accessible and replacing coal, electricity and nuclear. The question is how can we do that? The sun is the key part of the solution since it provides 8000 times the energy needed directly to the planet. However, the problem is cost and solar infrastructure. One student in our group raised a good question regarding how to persuade people to use renewable energy when it is more expensive. The answer is that some people just want it. Similarly to why we buy an iPhone over a cheaper phone – we just want it, not necessarily because it has financial value.
Moreover, we have learnt more about how digital transformation has changed the supply chain at Fronius. The key success factors are customers and suppliers. The whole thing starts from the customer purchase order in Electronic Data Interchange (EDI) which will translate Enterprise Resource Planning (ERP) from customer to the ERP of the company. Many activities in the company are done through e-platforms such as procurement, invoicing and credit notes, which are paperless and help to facilitate these business processes. In their warehouse, the company have IWACS vs Manufacturing Executing System (MES) – increased machine utilisation and maintenance programmes.
In the afternoon, we headed to the BMW Group Plant in Steyr. This plant is where BMW Group’s diesel engines are developed, as well as its three, four and six-cylinder diesel and petrol engines. On average, an engine will roll off the assembly line every 14 seconds. Eighty percent of the processes in this manufacturing plant are automatic. And to avoid mistakes on the assembly line, they use pick-to-light systems which will direct staff to which part is needed. After assembly, the engines have to pass premium quality tests.

Fronius International Plant with solar panel on the roof top
.
Plant tour and Q&A session
Dinner time@ Saloon 5
Categories & Tags:
Leave a comment on this post:
You might also like…
Keren Tuv: My Cranfield experience studying Renewable Energy
Hello, my name is Keren, I am from London, UK, and I am studying Renewable Energy MSc. My journey to discovering Cranfield University began when I first decided to return to academia to pursue ...
3D Metal Manufacturing in space: A look into the future
David Rico Sierra, Research Fellow in Additive Manufacturing, was recently involved in an exciting project to manufacture parts using 3D printers in space. Here he reflects on his time working with Airbus in Toulouse… ...
A Legacy of Courage: From India to Britain, Three Generations Find Their Home
My story begins with my grandfather, who plucked up the courage to travel aboard at the age of 22 and start a new life in the UK. I don’t think he would have thought that ...
Cranfield to JLR: mastering mechatronics for a dream career
My name is Jerin Tom, and in 2023 I graduated from Cranfield with an MSc in Automotive Mechatronics. Originally from India, I've always been fascinated by the world of automobiles. Why Cranfield and the ...
Bringing the vision of advanced air mobility closer to reality
Experts at Cranfield University led by Professor Antonios Tsourdos, Head of the Autonomous and Cyber-Physical Systems Centre, are part of the Air Mobility Ecosystem Consortium (AMEC), which aims to demonstrate the commercial and operational ...
Using grey literature in your research: A short guide
As you research and write your thesis, you might come across, or be looking for, ‘grey literature’. This is quite simply material that is either unpublished, or published but not in a commercial form. Types ...