Day two of the Executive Logistics and Supply Chain MSc study tour: “The best or nothing” in Thailand – Cranfield meets TAAP (Mercedes Benz)
10/05/2018
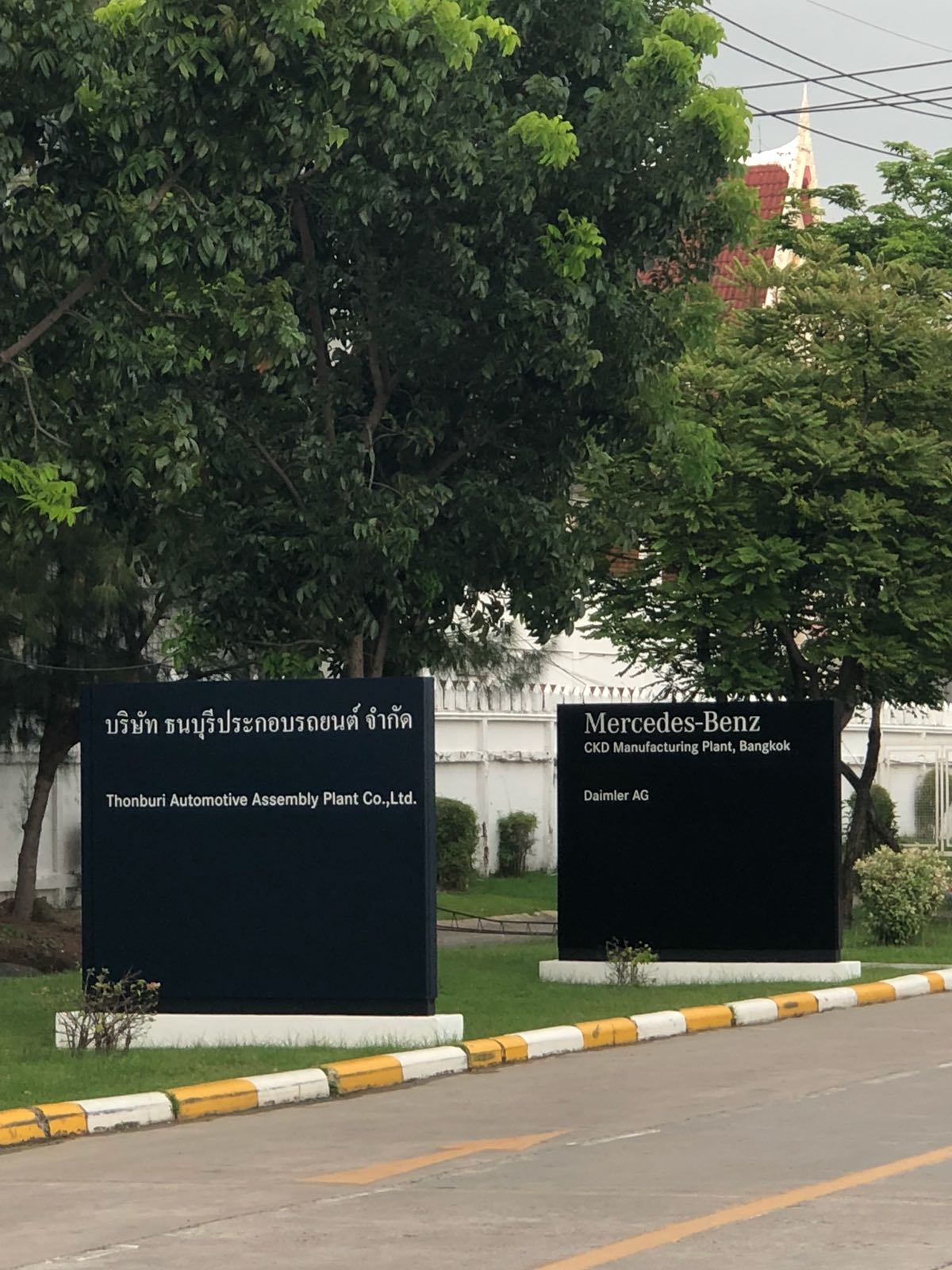
For the second day of the tour we woke to a magnificent, highly-impressive thunderstorm which set the tone for the much anticipated visit to Thornburi Automotive – the contract manufacturing organisation that produces the equally impressive Mercedes cars desired throughout the world.
Thailand has significant expertise in car production producing two million cars a year, of which half are exported. Thornburi is not in this mass market but focused on the top-end marque to satisfy the local market. They’ve been working with Mercedes since 1950 which shows what a great partnership they have.
Mercedes’ trust in them has been well-placed as they have shown themselves able to continue producing the required quality despite ramping up production by over 30% last year and 300% since 2014! This proven agility has allowed them to adjust too, to the changing product mix as models are launched and withdrawn.
Mercedes strictly control the design of the products and the quality of the components but still source 40% locally with Thai tax regulation providing an incentive. When it comes to process however, Thornburi is its own master and able to innovate and respond to local market requirements. Nowhere was this clearer than the extra focus put on waterproofing and rain testing; a reminder of the morning’s thunderstorm. By restricting automation Thornburi have given themselves the agility and adaptability to adjust rapidly to the market.
After an engaging presentation that triggered a host of questions, we headed off on a tour of the factory, carefully timed to avoid their break. The facility is large, operating from a site of some 200,000 square meters and evidence of continuing investment in further buildings was clear. It was great to learn of their awareness and consideration of their neighbours; in particular the collaboration with a neighbouring school.
The production facility itself was as immaculate as you now expect from a modern plant and we saw the goods-in, quality control, and stores from which forklift drivers delivered the necessary components to each line and station. After the welding and paint shop, the bodies move through to competing lines adding trim and sub-assemblies to produce a product ready to be finished, polished up and quality checked ready for the eager customer.
By having comprehensive, certified quality and environmental management systems in place they have ensured that the product continues to meet the requirements of a very demanding clientele. Of course, that does mean that the staff canteen is a little larger than we may be accustomed to in the UK.
Perhaps Thornburi’s success is helped by the beneficent calm inspired by the Buddhist shrine that welcomes you on arrival..
.
Categories & Tags:
Leave a comment on this post:
You might also like…
Meet Mendeley: a powerful referencing tool that does the hard work for you!
Are you looking for a way to manage your references, create in-text citations and reference lists for your assignments or thesis? If so, you may wish to consider using Mendeley. What is it? Mendeley is ...
Adding documents to your Mendeley account
To make the most of a Mendeley account, it is useful to create and maintain a ‘Library’ of references. You can add references and documents to this Library in a number of ways: 1) Drag ...
Choosing the right reference management tool for you…
Are you thinking about using reference management software to help you manage your references? The Library is here to help you. While Mendeley has been our go-to reference management software for some years, we've recently ...
Cranfield Seed Fund recipient, Cosysense, are using AI to solve air conditioning problems and provide a net zero alternative
If you’ve ever worked in an office environment you’ve probably been involved in, or overheard, a conversation about the air conditioning. Well, it’s no surprise it’s a common complaint when research shows that up ...
An Eye-Opening Journey in Advanced GIS & Remote Sensing at Cranfield University
My experience in the Advanced GIS and Remote Sensing course at Cranfield University was nothing short of transformational. From day one, the course was designed to provide both technical expertise and real-world applications. What ...
EBSCO databases – User interface changes
EBSCO has recently introduced a new user interface which you will see when you access any of our EBSCO databases - Business Source Complete, EBSCO eJournals and eBooks, GreenFILE, PsycARTICLES and PsycINFO. If you've used ...