Methods, Methods, and Methods… Part 1 of 2
30/08/2017
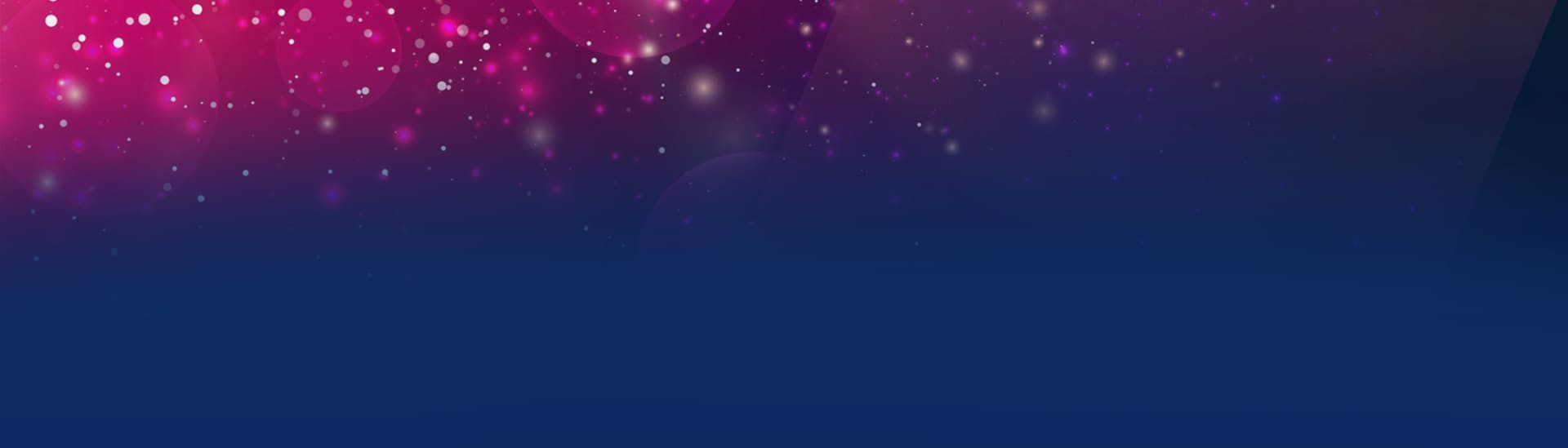
How many times has a senior executive approached you and said, “We’re going to use Method ‘X’ to improve our business processes”?
What flies through your mind when you hear this:
- “I didn’t know our business processes needed improving.”
- “What’s Method X?”
- “Why Method X, why not Method ‘Y’, and how do we know it’s the right method?”
- “This is just another excuse to cut costs and ‘save’ money.”
- …..
On our travels, we often come across this challenge – “We’re going to do ‘Demand Management’ using Method ‘X’”. Our usual response is to unpick this requirement statement to understand two concepts – Demand Management and Method X.
Demand Management:
Often we see organisations focusing on what comes in through the “front door” – in many cases the Contact Centre. In the police, for example, this may be a good place to start, or may be the easiest place since usually there is much more data (i.e. evidence) captured around handling calls and managing incident and response and on into crime and investigation. However, at a recent Evidence-based Policing Conference, an ACC from a large force explained “… only 19% of our demand is crime, 81% is dealing with vulnerability”. If we look carefully though, the vulnerability work should have originated somewhere in a call for service – so tracking demand (by developing a “Flow Model”) from call to resolution should be a reasonable context to examine.
Furthermore, an organisations’, systems’ or process’ “Purpose” needs to be well articulated and understood, and translated into activities that we can measure at the front-line. Only with a clear sense of purpose can we consider the different types of demand characterised below.
So, keeping with the Police example, demand flowing through the front door (calls, e-mails, web, etc.) can be characterised as “value” (i.e. demand we want to work on), “waste” (i.e. demand that should not be coming to us, but should be dealt with elsewhere) or “failure” (i.e. demand we generate by not processing the flow of work appropriately) demand. In our approach, we recommend you visualise these types of demand using a “Measurement Model” – the idea being, if you can see it, you can do something about it, but this has its challenges (see Part 2 of this blog).
Why characterise demand in this way – well if we want to manage demand, we need to resource to it appropriately. But it would be a costly exercise if we simply resource processing of waste and failure demand (along with value demand) – best try to remove them. What causes waste and failure demand? Let’s start with failure demand (because it’s easier to handle), then look at waste demand (which usually involves some form of partner or other agency working).
Failure Demand:
If we can understand what causes it, we can do something about it. Again, let’s look at the police example as we can be quite specific rather than use generalities.
We have observed that failure demand can be generated by at least the following:
- Missing or incorrect “Critical To Quality” (CTQ) data from the stage before (e.g. correct address details not collected in contact centre and unit cannot get to correct location)
- Extended “Throughput” times (e.g. response times), causing the person requiring the service to make a second or more requests into the contact centre
- Build-up of “Work In Progress” (WIP) at one or more stages in the process, possibly because of bottlenecks in the process, causing either extended Throughput Times as per 2 above, or causing people to rush and skip certain steps and miss CTQ data per 1 above
- Bottlenecks being caused either by under-resourcing or by controlled random variation in demand, in all process stages, in outcomes and in resourcing (often a major issue, but seldom addressed properly)
- Bottlenecks moving around between stages caused by so-called agile resourcing or by uncontrolled random variation in demand, in all process stages, in outcomes and in resourcing (often a major issue, but seldom addressed properly).
So a solution simply reaching for re-designing the so-called bottleneck is only part of the story – and without understanding the root-cause of the failure demand, could add costs and reduce effectiveness of the process.
Waste Demand:
We have observed that waste demand can be generated by at least the following (and there will be some cross-over with failure demand in some cases):
- Failure in another process – e.g. high-levels of calls coming into 101 number not being answered and public turning to 999 calls since they know these will be answered.
- Ill-informed customers or members of the public – e.g. a member of the public calls police in the case of a disturbance in the community. Perhaps, if these kinds of calls are frequent, then engaging with the community and asking them to assist in generating an environment of reasonable behaviour might be more effective
- Extended Throughput Times – e.g. police dealing with mental illness when actually a properly trained ambulance crew might be better, or hospital or council services may be a better alternative to a custody suite.
- Demand generated by regulators and oversight bodies – e.g. in the case of Police, HMIC (Her Majesty’s Inspectorate of Constabularies, PCCs, Home Office etc.). In our travels, without exception, in any sector – private or public – we see that regulators are “way behind the A-ball” when it comes to the organisations they are there to regulate. I have some ideas why this is the case (another blog perhaps), but the critical impact is that they can generate masses of waste by ill-thought imposition of procedures, requests for information, etc.
- Other agencies/bodies calling for service, rather than dealing with it themselves – e.g. in a stressful situation, say in a local council customer service centre, perhaps there may be better ways of handling agitated customers rather than pointing to signs about abusing staff and calling the police?
Value Demand:
Demand Management is not just about removing waste and failure demand. For certain process types like Trouble-to-Resolve – T2R – (see generic process types in previous blog https://cranfieldcbp.wordpress.com/2017/02/20/the-future-of-operational-performance-management-part-2/) massive savings can be achieved by working out ways to reduce so-called value demand. This often involves looking at the wider System in which our processes are operating , as well as Purpose. We’ll use some specific examples to help illustrate this.
- In New Zealand, by increasing the number of preventative activities, there was a direct impact in reduced crimes of “Dishonesty”, saving crime and investigation resources as well as reducing costs to society
- In Manchester, by applying preventative policing in student accommodation areas at the start of academic years, the volume of burglaries was significantly reduced, again generating savings in crime and investigation and cost to society
- In a global investment bank, by changing the way non-emergency software fixes were applied, the start of week peaks in problems reported to the IT Help Desk were vastly reduced, essentially releasing more IT Operations capacity to improve the quality of software changes.
- In a global telecommunications supplier, by changing the positions of distribution boxes (or making them weather-tight) on top of telephone poles as part of normal maintenance work over the summer, the regular seasonal January peak in faults was completely removed, saving £ms for the supplier and vastly improving customer service.
In our second of these two blogs, we’ll look at the Methods that can be used to Manage Demand – and from what we’ve seen, by applying a blend of methods it’s definitely not been a waste of time.
Categories & Tags:
Leave a comment on this post:
You might also like…
Keren Tuv: My Cranfield experience studying Renewable Energy
Hello, my name is Keren, I am from London, UK, and I am studying Renewable Energy MSc. My journey to discovering Cranfield University began when I first decided to return to academia to pursue ...
3D Metal Manufacturing in space: A look into the future
David Rico Sierra, Research Fellow in Additive Manufacturing, was recently involved in an exciting project to manufacture parts using 3D printers in space. Here he reflects on his time working with Airbus in Toulouse… ...
A Legacy of Courage: From India to Britain, Three Generations Find Their Home
My story begins with my grandfather, who plucked up the courage to travel aboard at the age of 22 and start a new life in the UK. I don’t think he would have thought that ...
Cranfield to JLR: mastering mechatronics for a dream career
My name is Jerin Tom, and in 2023 I graduated from Cranfield with an MSc in Automotive Mechatronics. Originally from India, I've always been fascinated by the world of automobiles. Why Cranfield and the ...
Bringing the vision of advanced air mobility closer to reality
Experts at Cranfield University led by Professor Antonios Tsourdos, Head of the Autonomous and Cyber-Physical Systems Centre, are part of the Air Mobility Ecosystem Consortium (AMEC), which aims to demonstrate the commercial and operational ...
Using grey literature in your research: A short guide
As you research and write your thesis, you might come across, or be looking for, ‘grey literature’. This is quite simply material that is either unpublished, or published but not in a commercial form. Types ...