3D Metal Manufacturing in space: A look into the future
26/07/2024
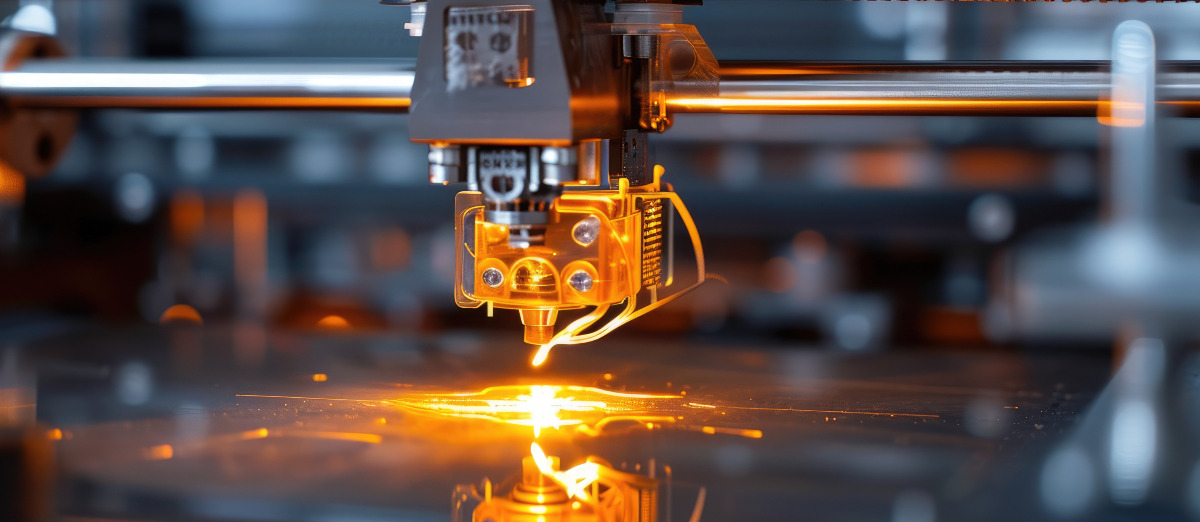
David Rico Sierra, Research Fellow in Additive Manufacturing, was recently involved in an exciting project to manufacture parts using 3D printers in space. Here he reflects on his time working with Airbus in Toulouse…
When you are offered the chance to work on a project at Airbus, one of the biggest companies in the aerospace industry, you don’t say “I’ll think about it.” So when I was fortunate enough to be offered work on a short-term, interdisciplinary project at Airbus HQ in Toulouse, France, I jumped at the chance! I was there to contribute my expertise in additive manufacturing to a team made up of people from all over Europe. It was rewarding and challenging in equal measure.
Creating an automated ‘space factory’
The goal of the project was to show that it was possible to create a fully automated ‘space factory’ for spare parts as part of the Star Tiger Initiative from the European Space Agency. We wanted to find out how to integrate two different printers – a Carbon Fibre Reinforced Plastics (CFRP) 3D printer and a metal 3D printer – in conjunction with robotic arms that assemble the parts after they’ve been printed. The project was a feasibility study to show that it was possible to produce, verify and assemble CFRP and metallic parts produced in the two printers, creating a modular part of a satellite antenna.
My role was to help find a solution for one of the main challenges in using a metal printer – finding the correct set of parameters and techniques to remotely remove a small, printed metallic part from the printer, and the separation of that part without additional tooling and little-to-no human interaction.
That meant first fully understanding the capabilities of the newly produced 3D metal printer, which was a replica of the one sent to the International Space Station (ISS) in January 2024. This was key, because we needed to be able to reliably produce metallic parts from it, modifying methods and parameters to meet our objectives.
The second challenge was to produce a small, metallic part which would be easily detachable from the base layer inside the printer in an automated process. Although it sounds a simple thing, this was a seriously complex task and presented a few headaches and frustrations!
In most 3D printers the part being built is secured to the substrate to provide a stable and reliable base for adding the next layer of material. This is why the metallic parts produced in 3D printers require additional tooling to separate the part from the substrate – in this case some kind of metal cutting equipment. However, additional equipment and resources are limited on the ISS, and this would also increase the complexity of the system. Given that one of the goals was to make the process fully automated, this was a real challenge for the team.
Collaboration, diversity and innovation made it unforgettable
The team was made up of people with vastly different backgrounds and experiences. Early on that meant a learning curve in terms of finding ways to work together, but ultimately that diversity of experience was an invaluable asset, with varied backgrounds and approaches uniting to address the complexity of the goals.
One of the most important takeaways from this project was to understand what it’s like to work with the support of a huge company like Airbus. They’re one of the leading players in the aerospace sector and have a broad range of knowledge about working with space-focussed projects.
On a personal level, my part of the project was filled with challenges and sometimes even frustrations, but the continuous support from the whole team at Airbus, and my supervisor at Cranfield, helped me succeed. At the end of the project we gave a demonstration of the process in front of ESA representatives. It was well received and a proud moment not only for me but for the whole team, who worked tirelessly to make sure that the project was a success.
I’m very grateful to have had the opportunity to work with Airbus. I was rewarded with wonderful experiences but also complex challenges and the enthusiasm for collaboration, desire for excellence and innovation made this project unforgettable.
Categories & Tags:
Leave a comment on this post:
You might also like…
Credibility, confidence and collaborative focus: The impact of studying for a sustainability apprenticeship at Cranfield
For participants on Cranfield’s Sustainability Business Specialist Apprenticeship, it doesn’t take long for their studies to start to have an impact, with that impact ranging from personal growth and career progression, to organisational effect ...
Meet Mendeley: a powerful referencing tool that does the hard work for you!
Are you looking for a way to manage your references, create in-text citations and reference lists for your assignments or thesis? If so, you may wish to consider using Mendeley. What is it? Mendeley is ...
Adding documents to your Mendeley account
To make the most of a Mendeley account, it is useful to create and maintain a ‘Library’ of references. You can add references and documents to this Library in a number of ways: 1) Drag ...
Choosing the right reference management tool for you…
Are you thinking about using reference management software to help you manage your references? The Library is here to help you. While Mendeley has been our go-to reference management software for some years, we've recently ...
Cranfield Seed Fund recipient, Cosysense, are using AI to solve air conditioning problems and provide a net zero alternative
If you’ve ever worked in an office environment you’ve probably been involved in, or overheard, a conversation about the air conditioning. Well, it’s no surprise it’s a common complaint when research shows that up ...
An Eye-Opening Journey in Advanced GIS & Remote Sensing at Cranfield University
My experience in the Advanced GIS and Remote Sensing course at Cranfield University was nothing short of transformational. From day one, the course was designed to provide both technical expertise and real-world applications. What ...