Translating manufacturing research into industry impact
15/10/2020
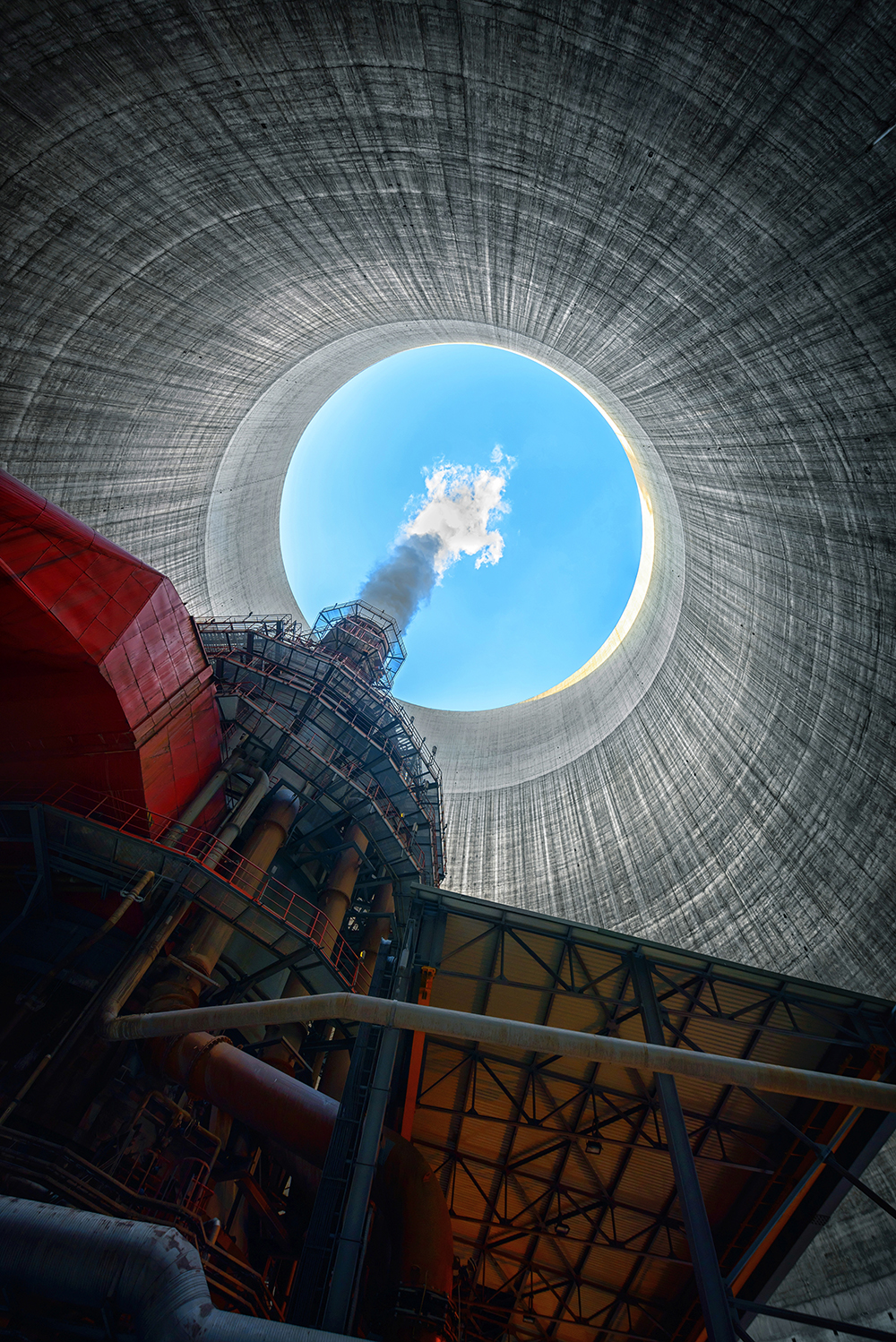
Andrew Storer, Chief Executive Officer, Nuclear AMRC
The Nuclear AMRC is part of the High Value Manufacturing Catapult, an alliance of seven leading manufacturing research centres backed by Innovate UK. Andy joined in 2015 from Rolls-Royce’s civil nuclear business. He is a Visiting Professor of Nuclear Manufacturing and Capability Development at the University of Sheffield. He sits on the Nuclear Industry Council, is Chair of the ‘winning UK business’ group, as part of the nuclear sector deal, and is the UK Generation IV international forum lead for manufacturing and materials. He is also a board member of the Nuclear Industry Association and the Nuclear Innovation Research Advisory Board.
What are the current challenges the industry faces?
Everyone in the energy sector is facing the same key challenge: how best to bring carbon emissions down while still delivering the energy the world needs at a fair cost. The nuclear industry – the most reliable source of low carbon energy – has to be at the centre of any solution but we know that the pace of innovation in the nuclear industry is considerably slower than its counterparts. Unlike the faster-paced automotive industry, where new models and innovations are brought out frequently, designs for new nuclear reactors can take more than a decade to develop. Introducing innovation into the sector can present a risk that many technology owners (vendors and developers) are not willing to take. Even where those innovations might help developers save millions of pounds, in the context of a £10 billion reactor programme that saving can seem insignificant compared to the perceived risk of the innovation. Too often developers and vendors will simply want to carry on with the tried and tested method they know.
This passion for the familiar affects every level of the industry. New build plants facilities typically replicate previous new builds as much as possible – the French reactors at Hinkley Point C are planned to be as close as possible a direct replica of those in Flamanville with Sizewell C to be as near as possible a replica of Hinkley Point C. Developers see it as much easier to continue with tried and tested designs, replicating existing manufacturing assembly set up across the globe. Inevitably that makes innovation (in an already slow-to-adopt industry) increasingly difficult.
Against this challenging backdrop, how do we introduce innovation – and how do we also introduce the UK nuclear supply chain?
As a nation we have some fantastic capabilities in nuclear design and manufacture and early stage research. Our universities and translational industrial research centres like the Nuclear AMRC are in many aspects world leading. Over the last two decades we have developed one of the most advanced nuclear submarines in the world, our waste management and decommissioning capabilities are admired globally. Our developments of fusion technology are truly ground-breaking and rightly gaining worldwide attention.
Sadly, for large new build developments the UK simply hasn’t exercised its manufacturing capabilities since the construction of Sizewell B in the 1980’s, meaning that gaps exist in current capability and capacity. The good news is that that could be about to change.
The creation of a UK Small Modular Reactor (SMR), on which the Nuclear AMRC is working alongside Rolls-Royce and other consortium members, is a huge opportunity for innovation. Likewise, the Government announced recently investment in the development of new Advanced Modular Reactors (AMRs) and fusion technologies. My team is supporting all of these projects. Innovation is essential for these new designs and, I hope, will prove much easier to introduce with no previous reactor safety case and operational plant to replicate.
The reality, of course, is that we are still a few years away from implementing innovations to the small and advanced technologies and there is a more immediate, ‘here and now’ challenge. We need existing reactors to deliver electricity, and we need the economic benefits that the UK supply chain can get from those current reactors and we need those large overseas technologies to be built, to replace the existing fleet by around 2030. In parallel, we also have to make sure that UK supply chains are ready for the design and manufacture of UK designed technologies, where we can then introduce innovation. We must translate research into industrial impact in today’s world while gearing up for tomorrow. If we get this right we can use the large reactors to help us fill gaps identified earlier, and scale up capability in readiness for UK technology.
Together with the Nuclear AMRC, companies are introducing innovation, but only in small areas in nuclear new build. If the country is buying-in overseas technology to build new nuclear reactors, what is the UK supply chain doing to harness our capabilities in other sectors?
One example is at Sellafield. Here we have one of the world’s largest decommissioning sites which needs to be managed and maintained. We have an operating fleet of 14 reactors providing 40% of the UK’s green energy and 20% of our electricity. We have developed a method for joining material together intended for a large reactor product but because that opportunity isn’t available to implement yet, we’ve transferred that research focus to a £4 billion taxpayer programme making waste container boxes – this could potentially save hundreds of millions of pounds in decommissioning costs. We aren’t simply waiting for our turn in the nuclear new build market. We are introducing our innovation into other parts of the sector and other sectors – oil and gas, petrochemicals, submarines and offshore renewables – and exploring how nuclear can play a bigger role in the low-carbon energy mix through applications such as industrial cogeneration and hydrogen production. Of course this also includes picking out capability and methods from other sectors like oil and gas and transferring them into application to the nuclear sector. Another example is how we have taken our Fit4Nuclear programme and developed it to Fit 4 Offshore Renewables with the Offshore Renewable Catapult.
There’s a well-known diagram called the Valley of Death – but I would rather it be renamed the Valley of Excitement.
It’s actually quite good fun translating from academia to industry where the best ideas can be converted into true national impact (even if a little frustrating at times, it is fun). Currently we sit between 3 and 6 on the technology readiness scale which runs from 0 to 9, so we’re taking ideas from academia and translating to industry and, where needed, pushing innovation and ideas into industry. The frustration comes when there is no industry sponsor such as Sellafield, EDF or Rolls-Royce to pull the ideas through and it’s just us pushing. When we do get new reactor designs, UK companies will be in prime position to help make them happen – it just needs Government to ensure these programmes continue.
What about the impact of Covid-19?
Covid-19 has had a huge impact on the supply chain and its ability to work and deliver contracts. It has also made us acutely aware of both the fragility and potential of our manufacturing base, born out by difficulties in delivery of UK produced PPE and, of course, the challenge to produce more ventilators for the UK where a consortium firms came together to show just what our manufacturers could deliver against a sharply focused goal.
We are in a global market working closely with other nations including China, France, the US and Canada, on joint initiatives. We now need to get into a ‘wartime mindset’ for energy. We need to become much more self-sufficient. With our ambitious target to be net zero carbon by 2050, we can’t keep dancing around the topic. We have 30 years to achieve this so we must go full throttle for wind, solar, hydrogen production and, of course, nuclear as a fantastic, reliable, clean energy. We need to be prepared to ensure energy security and affordability of supply for the UK, just like the real examples of PPE and ventilators.
The Coronavirus has shown just how fragile an island we are. As part of the HVM Catapult, we were heavily involved in the VentilatorChallengeUK programme which delivered more than 13,000 ventilators in 12 weeks alongside a host of manufacturing companies. It was needed because, when Covid arrived here, the UK just didn’t have the capability to deliver. This situation should force us to look at specific capabilities we’ve allowed to erode and need to bring back.
Covid really shines a light on the need for the UK to be able to produce products and not be so reliant on others. One of the challenges in the nuclear industry has been a somewhat stop-start approach from Government. To develop the supply chain and emerge stronger, we need Government to help stimulate the supply chain by confirming that programmes that are already committed will go ahead and making longer term decisions on future technologies. If Government shows its confidence and commitment that will give the supply chain the confidence to invest and stimulate further innovation.
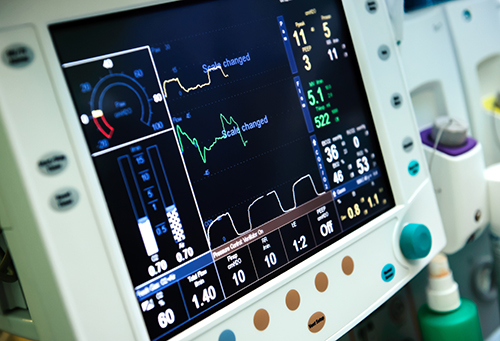
What’s next?
We still have a lot more to do. More than ever, the UK nuclear industry needs to work as one, building on the good things across the sector and not just reinventing everything in silos. Part-funded by the UK government and the European Regional Development Fund, the Nuclear AMRC is working to make sure that new nuclear reactor designs can be turned into practical engineering solutions, using advanced manufacturing techniques to reduce cost and maintain the highest standards of quality and safety in the UK supply chain. This will ensure UK firms have a chance in the international market and are seen as leaders in technology.
The focus remains to cut the UK’s greenhouse gas emissions to net zero by 2050. With new nuclear build solutions coming on stream and the costs of delivery falling, everyone acknowledges that nuclear must be a key part of our energy mix. We need to make sure our UK supply chains are ready and able to deliver.
In terms of nuclear next steps, we really hope a UK technology will be pushing forward in the next 6 months with the right level of investment and government confidence. There is a lot of talk about levelling-up the economy, especially across the north, and this is very important but we also need to level-up the playing field for smaller companies to thrive. Enabling small companies to gain easy access to innovative solutions without huge investment is a top priority for my team. That’s why my centre has been looking for new ways to connect with more firms to help give them a performance boost.
The Nuclear AMRC is about to launch a new facility in Derby for electrical controls and instrumentation. This is in addition to our existing digital centre, which is also based in Derby. We continue to develop our module facility in Birkenhead, taking shipbuilding methods and trying to utilise in the new nuclear sector to take cost out of the construction / assembly phase. Not forgetting the constant challenge of implementing latest joining and machining capabilities from our Rotherham facility.
Still a huge amount to deliver and impact to create but given the current focus on delivering economic value for Britain our mission ‘to help UK companies win’ has never been more relevant.
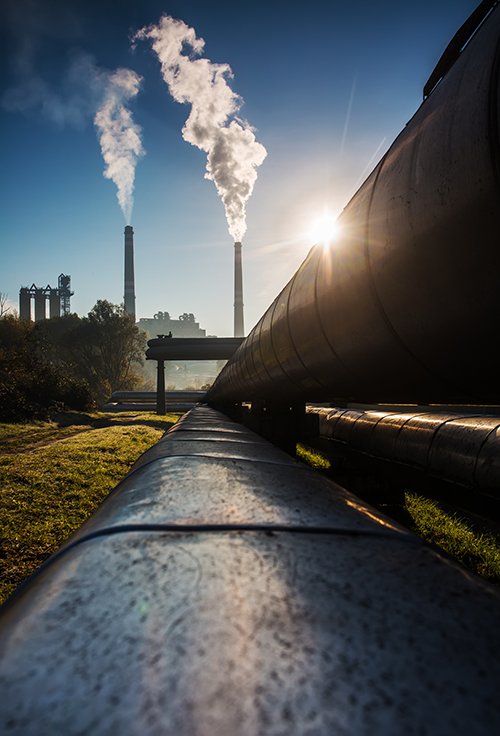
For more information and how to register for our Manufacturing and Materials week visit: https://www.cranfield.ac.uk/manufacturingweek
Categories & Tags:
Leave a comment on this post:
You might also like…
Mastering the art of revising your writing
You’ve done the research and written your first draft. Now it’s time for one of the most crucial jobs as a writer - revising your writing to ensure your reader does not have to work ...
A ‘hands-on’ take on warehouse design as part of my Logistics and Supply Chain MSc
As part of my core module for my Logistics and Supply Chain Management MSc, I had the amazing opportunity to work on a warehouse design project a few weeks ago. The problem statement for ...
Thinking about your literature review?
As part of your PhD or Master’s thesis, you will probably have to write a literature review. A successful literature review will offer an analysis of the existing research in your field, demonstrating your understanding ...
A beginner’s guide to sourcing a company beta
Beta is the measurement of a company’s common stock price volatility relative to the market. If you’re trying to find a current beta for a company there are a number of places to look. These ...
Credibility, confidence and collaborative focus: The impact of studying for a sustainability apprenticeship at Cranfield
For participants on Cranfield’s Sustainability Business Specialist Apprenticeship, it doesn’t take long for their studies to start to have an impact, with that impact ranging from personal growth and career progression, to organisational effect ...
Meet Mendeley: a powerful referencing tool that does the hard work for you!
Are you looking for a way to manage your references, create in-text citations and reference lists for your assignments or thesis? If so, you may wish to consider using Mendeley. What is it? Mendeley is ...