Manufacturing 2075
27/11/2019
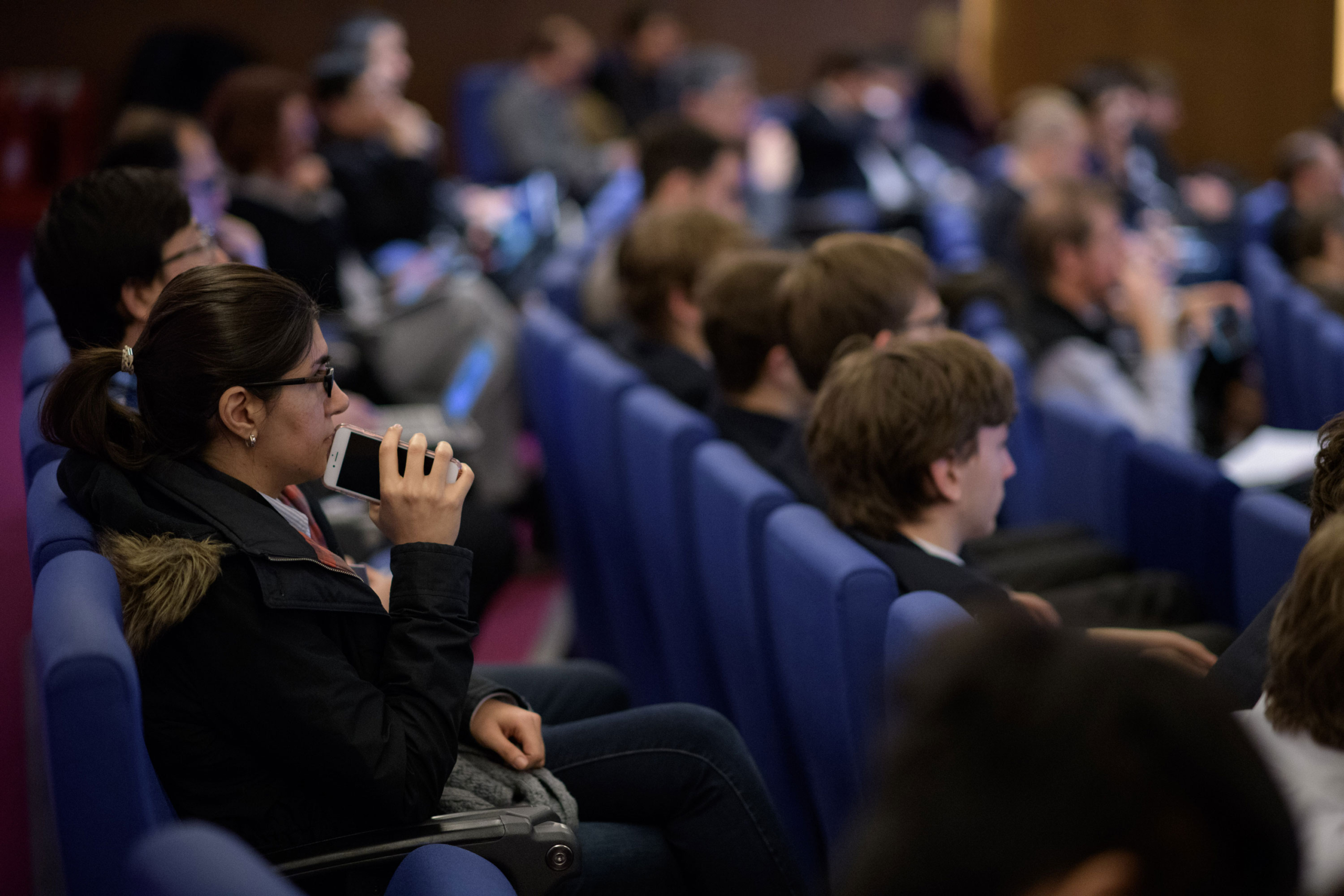
Switching to sustainable alternatives is an imperative – but needs to be done in a clear-headed way, informed by a full knowledge of implications. This is nowhere more important than in manufacturing, the global machinery for transmuting natural resources into what’s useful, what’s needed.
Our work at the Natural History Museum on the transition to electric vehicles has illustrated the bare bones of the kinds of problems the world faces.
Meeting the new UK electric car targets for 2050, we’d need to use almost double the world’s entire annual cobalt production; nearly all the world’s production of neodymium; three quarters of lithium, and at least half of the copper. Then there’s the electricity involved to provide the charge for each of the 252.5 billion miles driven by UK cars every year, meaning a 20% increase in UK-generated electricity.
This is why Manufacturing 2075 (4 December 2019) is focused on the practical, operational issues around sustainable manufacturing. We’ve gone past the point of good principles and intentions, we need to have a stronger grasp of the balance of issues, and to start implementing what works.
Most important for the sector will be future ways of working with the providers of commodities. There needs to be more collaboration and connection over the forms of commodities, what’s needed as technologies develop. Traditionally, for example, a material like zinc would be taken out of the ground and sent straight to a blast furnace to be turned into a metal. But maybe what a new product under development might need is zinc as a carbonate or a sulphate. There’s a disconnect in the market.
The problems we face now – and for the future – are often not around running out of a raw material, but that the particular commodity is not available in the forms actually needed. So there is a squeeze in the market, short-term shortages and price hikes. What’s needed is more of a Just-in-Time process involving raw materials to prevent sudden squeezes on supply, and that will mean manufacturers looking to improve the diversity of forms of material and their supplies. With a resource like cobalt, political instability in Central Africa would lead to an instant cut in around 70% of supply.
Every part of the chain, from design to the mining and metals industries, need to be talking to each other to make the cycle genuinely sustainable. And ultimately that means manufacturers looking at the end-of-life stage of products, re-shaping their relationships with suppliers to be part of the circular economy, reducing the reliance on what can be dug from the ground, and what can be re-used and re-purposed, not lost into the waste stream.
Professor Richard Herrington, Head of Earth Sciences, Natural History Museum, www.nhm.ac.uk
Industry and thinkers come together for Manufacturing 2075 at Cranfield University on 4 December 2019 – a full list of speakers is here: www.cranfield.ac.uk/events/manufacturing-2075-landing
Categories & Tags:
Leave a comment on this post:
You might also like…
A ‘hands-on’ take on warehouse design as part of my Logistics and Supply Chain MSc
As part of my core module for my Logistics and Supply Chain Management MSc, I had the amazing opportunity to work on a warehouse design project a few weeks ago. The problem statement for ...
Thinking about your literature review?
As part of your PhD or Master’s thesis, you will probably have to write a literature review. A successful literature review will offer an analysis of the existing research in your field, demonstrating your understanding ...
A beginner’s guide to sourcing a company beta
Beta is the measurement of a company’s common stock price volatility relative to the market. If you’re trying to find a current beta for a company there are a number of places to look. These ...
Credibility, confidence and collaborative focus: The impact of studying for a sustainability apprenticeship at Cranfield
For participants on Cranfield’s Sustainability Business Specialist Apprenticeship, it doesn’t take long for their studies to start to have an impact, with that impact ranging from personal growth and career progression, to organisational effect ...
Meet Mendeley: a powerful referencing tool that does the hard work for you!
Are you looking for a way to manage your references, create in-text citations and reference lists for your assignments or thesis? If so, you may wish to consider using Mendeley. What is it? Mendeley is ...
Adding documents to your Mendeley account
To make the most of a Mendeley account, it is useful to create and maintain a ‘Library’ of references. You can add references and documents to this Library in a number of ways: 1) Drag ...