The Future of Aviation: Aircraft Electrification
06/02/2020
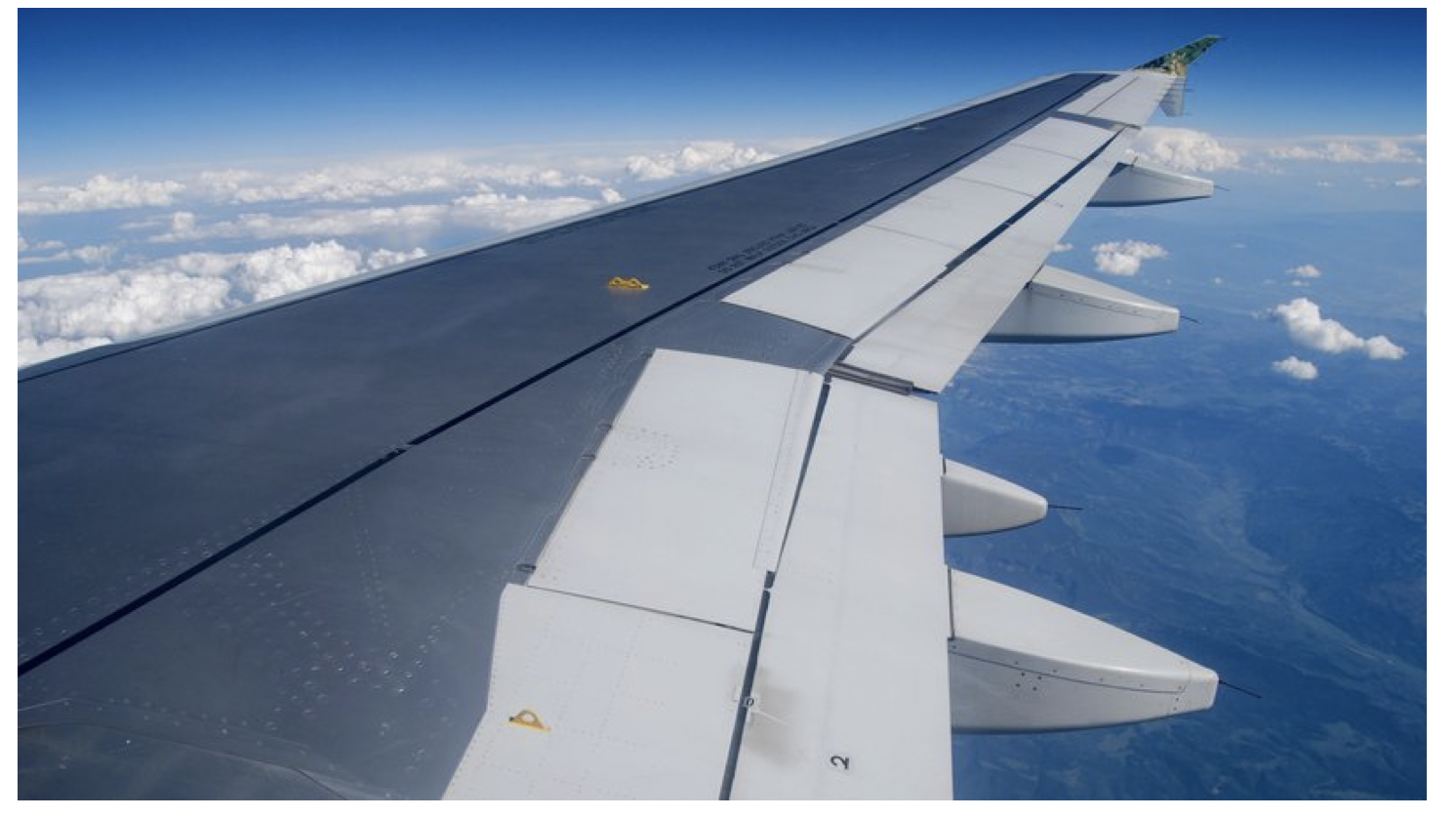
Introduction – The need for electric propulsion
In the automotive industry, electrification is developing at a fast rate. In the UK, both electric and hybrid cars are becoming a common sight on the roads, as well as electric charging ports in car parks. Electric vehicles offer a better solution towards a cleaner, greener environment than their diesel/petrol counterparts, as well as reducing noise pollution for those living in busy residential areas. So, when will air travel and air freight follow this electric journey?
Certainly, aircraft emissions degrade air quality and have an increasing effect on global warming as most emissions occur at high altitudes. According to the European Union [1], aviation accounts for approximately 3% of the EU’s total greenhouse gas emissions, and more than 2% of global emissions. Although air travel currently accounts for only a small portion of global emissions, air travel is recognized as one of the fastest growing contributors as elucidated in a recent study in the Atmospheric Chemistry and Physics journal, but by what mechanisms is aviation actually affecting the climate?
Aircraft engines do not only produce plenty of CO2, but also exhaust nitrous oxides, NOX, fine particulate matter, PM25, and ozone, O3. CO2 emissions are the most significant contributor to climate change and have the same effect regardless of altitude emission. However, at higher altitudes, NOX emissions are particularly effective in forming O3, thereby causing a greater global warming effect than would be the case at lower altitudes.
To put this into perspective, if you’ve ever played with a Carbon Footprint Calculator and plugged in a return trip from London to New York, this trip balloons your carbon footprint by more than 2000 pounds of CO2, nearly equivalent to the level of emissions incurred by heating an average European household for an entire year [2]. Reducing the CO2 impact of aircraft should be addressed early on, as future regulations may impart even stricter regulations on environmental targets that will only be achieved by the use of the latest, and most expensive, technologies.
Hence, there is a clear incentive for cleaner, greener air mobility: the reduction of CO2, NOX, PM25 and O3 emissions, reduced noise and fuel consumption. Currently, we have reached a plateau in terms of improving aircraft fuel efficiency and reduced emissions. By introducing electric battery-powered aircrafts, an opportunity exists to potentially reduce harmful emissions even further and to make air travel quieter for urban areas, but is electric flight actually possible given the technological challenges?
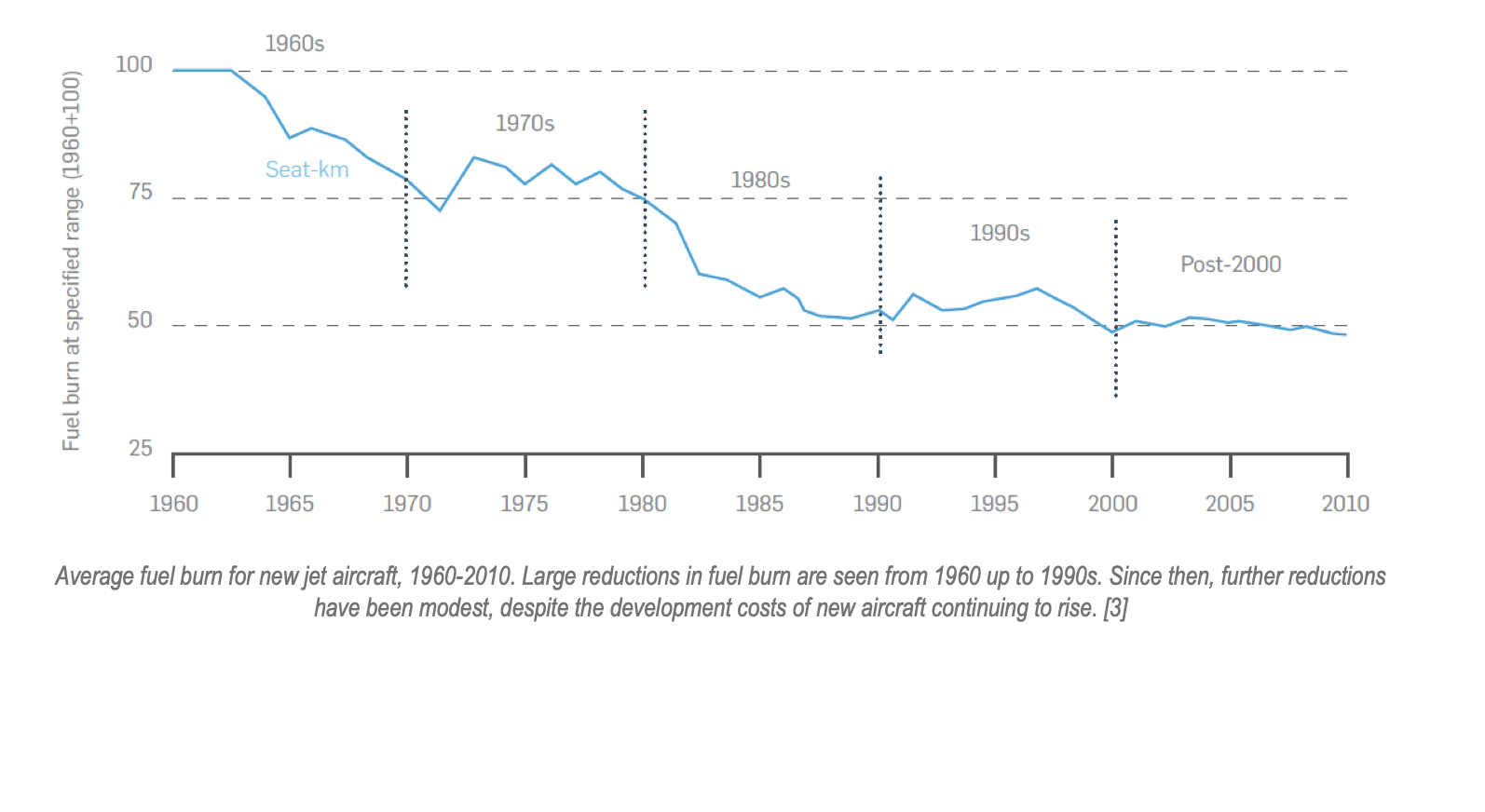
Average fuel burn for new jet aircraft, 1960-2010. Large reductions in fuel burn are seen from 1960 up to 1990s. Since then, further reductions have been modest, despite the development costs of new aircraft continuing to rise. [3]
Electric innovations: past, present and future
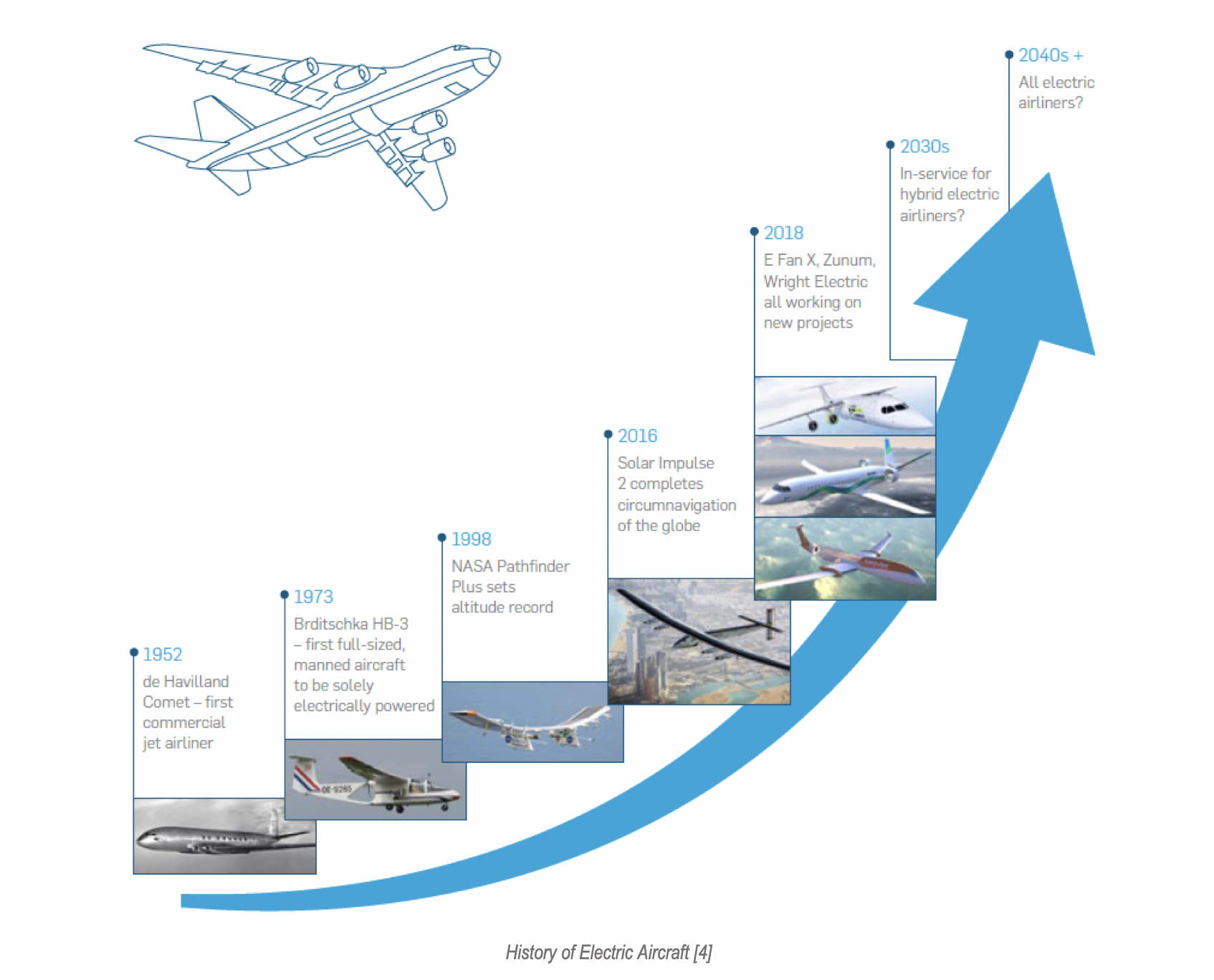
Many industry giants are playing their part to research and develop new prototypes and test concepts in electrification. Commercially, the Airbus A350 and Boeing 787 increasingly use battery power for several of their on-board systems to form an approach described as the ‘More-Electric Aircraft’ (MEA), whilst simultaneously developing methods for progression towards full electric propulsion. The strategy is to begin with a hybrid option first, with energy still provided by hydrocarbon fuels, and then progressing to an all-electric system with batteries to provide energy for propulsion.
In technical terms, the main critical challenge that projects like the Airbus E-Fan X, Zunum Aero and Wright Electric are faced with is the power-to-weight ratio or specific power. Considering an all-electric system, a battery with greater energy density than those currently available, which are also effective, reliable and have a long life, are required. Historic trends and current understanding of aircraft development cycles suggest that battery technology will not be available until the 2030s to allow full incorporation at current aircraft scales.
Potential propulsion system architectures
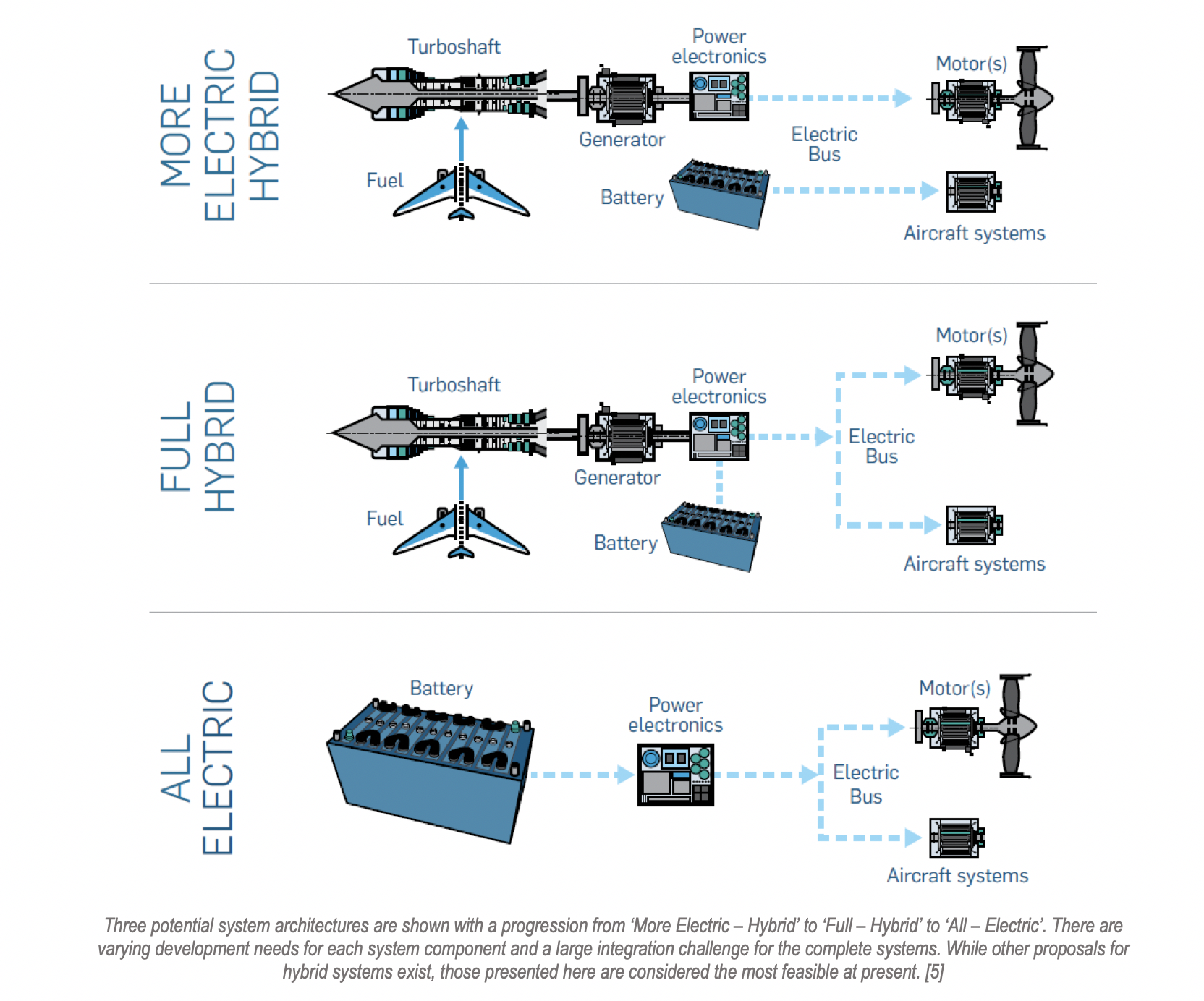
Three potential system architectures are shown with a progression from ‘More Electric – Hybrid’ to ‘Full – Hybrid’ to ‘All – Electric’. There are varying development needs for each system component and a large integration challenge for the complete systems. While other proposals for hybrid systems exist, those presented here are considered the most feasible at present. [5]
In the short term, we will probably witness a ‘More Electric-Hybrid’ commercially sized aircraft rather than an ‘All-Electric’ alternative. This ‘More Electric-Hybrid’ version could deliver real benefits through reduced emissions and allow for the development of motors and power electronics for the transition to fully electric operation. Let’s examine, on a system level, what a hybrid powered solution might look like.
Using the existing gas turbine, with traditional jet fuel (kerosene) mixed with biofuels, to drive an electric generator makes for an existing and well-understood solution. However, a new power electronics system is likely to be required to control and transfer the electrical energy to electric motors to provide thrust.
If batteries are used to power the remaining systems on the aircraft, we’ve got a ‘More Electric-Hybrid’ solution. The power available from the generator and batteries can be combined to power all aircraft systems to form a ‘Fully-Hybrid’ solution with each means of energy supply augmenting the other in different ratios during different flight phases, but if kerosene is still the source of energy, then where does the reduction in emissions come from?
In this scenario, the aircraft’s flight is affected by the varying thrust requirements needed for take-off, climb, cruise, and altitude changes. Current jet engines are designed to operate in all conditions, but do not always function optimally and efficiently in all cases. In a hybrid solution, the gas turbine could be isolated from changes in operational conditions and continuously run at an optimised speed to power an electric generator, which then drives the power electronics that provide electrical energy.
The main danger in this scenario is relying on unproven power distribution systems and electric motors. Indeed, one of the stated objectives of the Airbus E-Fan X program is to address this uncertainty with regards to electric power systems. Further advancements can be made by switching the kerosene-powered gas turbine and generator to battery power, thereby forming an ‘All-Electric’ system. In this case, the power electronics used for the hybrid solution will need to be adapted, but the propulsive element would not need to be changed.
A 50kg electric motor
Siemens developed a 50 kg electric motor SP260D that delivers 260 kW—five times more than comparable hybrid electric propulsion systems of equal weight. However, this is a long shot compared to the power required for a commercial aircraft to fly at acceptable speeds, typically in the order of two to 50 megawatts. Nonetheless, Siemens established its electric propulsion systems business through the development of the eAircraft program, now acquired by Rolls Royce.
So with improved technology, can enough power be generated? Currently, the answer to this question isn’t clear, keeping in mind the overall aircraft weight, safety considerations for electrical systems, wiring routes, electrical interference, and the thermal environment created by batteries.
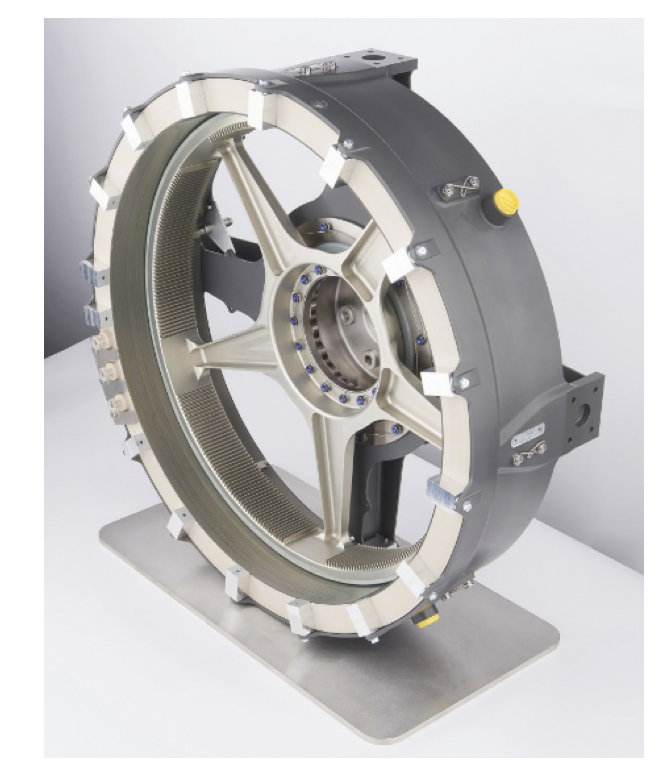
A high aspect-ratio wing design
Aircraft wings are designed to withstand aerodynamic loads and carry jet fuel distributed across the span. For an electric aircraft, would there be any benefit of carrying batteries within the wings instead?
One positive side-effect of electrification would be that the wing’s mass remains constant during flight (unless using lithium air batteries), creating novel opportunities for aeroelastic tailoring and aerodynamic optimization by allowing wings to become longer and thinner (better lift-to-drag ratio). A current challenge of designing long and slender wings for the conventionally fuelled is the onset of ‘aeroelastic flutter’, an unstable interaction between airflow and the wings elasticity causing build-up of oscillations and potential wing failure. With strategically placed batteries, thinner and longer wings could emerge as a viable design that doesn’t succumb to flutter, thereby improving aerodynamics and paving the way for radically different aircraft configurations.
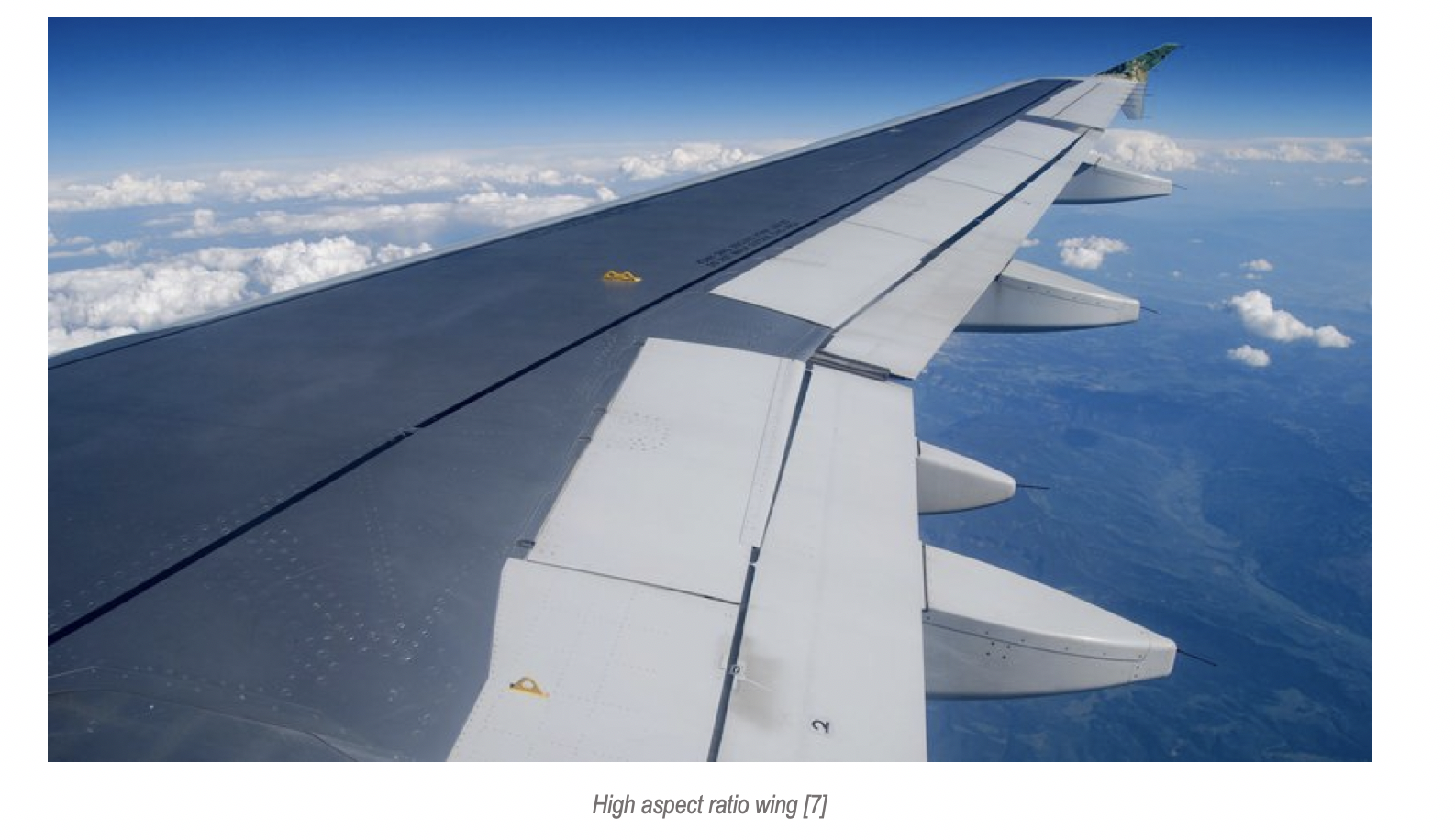
The need to reduce aircraft mass
What happens to the weight of the airframe in a move towards hybrid or full electrification? In a hybrid system, the full propulsion and electrical system, combined with all the technical operation equipment inside the aircraft, will probably increase the mass of the airframe. Furthermore, as the aircraft is no longer shedding mass via fuel burn during flight, the landing weight of aircraft is likely to be higher than it is today. To compensate for these effects, reductions in the airframe mass are probably required to facilitate a fully electric system. Indeed, designing lighter airframes is a huge challenge, putting great requirements on future research on materials science to determine the full capabilities of next-generation metallic alloys and fibre-reinforced plastics.
Funding resources
The best solutions often come from coordinated efforts to ensure a collaborative, knowledge-sharing approach that leads to conformity in standards. The UK is a major player in aerospace research and development and is involved in extensive research networks, partnerships, and bids to numerous funding bodies working on developing the technology for the future of air travel.
These funding bodies include the Engineering and Physical Sciences Research Council (EPSRC), as well as the Aerospace Technology Institute (ATI). They have been established between industry and the government to develop the UK’s technology strategy through £3.9 billion of investment. Another influential body is the Air Transportation Systems Lab, which collaborates on research projects with the UK and overseas universities.
Lastly, the largest European research program developing innovative technologies aimed at aircraft emission and noise reductions, known as the Clean Sky Initiative, has a €4 billion budget and has backed several projects like Airbus’ BLADE and Safran’s Contra Rotating Open Rotor engine.
Regulation
There is a need for new regulations regarding the emerging technologies, platforms and systems related to electrification. Firstly, as new technologies are created in the field of electric aviation, each technology will need regulatory backing to determine the airworthiness of the technology. This is critical to establish broad regulatory acceptance for enabling technologies like high-power batteries, voltage distribution systems and boundary layer ingestion.
Subsequently, regulation will be critical to enable new platforms. Regulation and certification procedures for radically new architectures such as distributed fans will be required to enable the full potential of Electrical Propulsion. As a first step, both the Federal Aviation Administration (FAA) and the European Aviation Safety Agency (EASA) are currently opening doors for Electrical Propulsion. For example, a key change in FAA Part 23 and EASA CS23 came into effect in 2017, allowing larger classes of general aviation aircraft to legally fly non-traditional engine types. This not only opens revenue potential for developers in general aviation, but this platform category is a key stepping stone to even larger architectures. There is however, a long journey ahead and regulation must keep a-pace with the technological evolution of electric aircraft.
In April 2018, these new regulations provided the opportunity for Siemens to test the Magnus eFusion at Matkópuszta airfield in Hungary, using a Siemens SP55D electric motor and a FlyEco diesel engine to allow for silent take-off and landing with an extended range. The full electrical propulsion system is developed by the Siemens eAircraft program. Furthermore, a Los Angeles-based company Ampaire recently demonstrated its electric hybrid propulsion system at Camarillo Airport in California with its maiden flight test in June 2019. Their technology was adapted to the Cessna 337 Skymaster and is already considered by some as the largest hybrid-electric aircraft to have ever flown.
There’s turbulence ahead
Certainly, the biggest challenge is integration. For example, when designers and engineers have new technologies ready for flight, how does the industry support in-service operation? As an aviation company, how will business models need to adapt over the next twenty years? When is the best time to start thinking about how to integrate these new business models with the shift in aircraft architecture? Even though some of these changes are still years away, it pays to contemplate the disruptive nature of these changes now, and to consider strategies of how the industry can ready itself to face up to these coming challenges.
Additional thoughts
Keeping in mind the potentially great opportunity aircraft electrification presents, Maintenance and Servicing Organizations (MRO’s) should be reconsidering their operations to address questions like what kind of physical infrastructure will be needed going forward? Topics for consideration range from how many spare batteries will need to be stored at airports and the most optimal location of recharging points to how long it will take for the batteries to be charged or changed in between flights. The latter will be a considerable consideration for airlines, as the aircraft will not be earning money when it is recharging. With regards to traffic control, what happens in the case of diversions and re-routing? Will regional electric aircraft take priority over long-range gas-powered aircraft? Or could quieter aircraft lead to additional airports in closer vicinity to cities, such that regional and long-range aircraft won’t share the same airspace? Finally, a major challenge will be instilling confidence in passengers about the safety of this new technology.
Conclusion – where do we stand?
The continuing growth of the aviation sector has buoyed production rates and has led Airbus and Boeing to establish themselves as the key players in the aviation market. This duopoly has only been reinforced by recent mergers and acquisitions of smaller operations (Bombardier and Embraer). The shift to electrification poses a risk to incumbents as this new paradigm in propulsion levels the playing field for new entrants into the market.
However, both incumbents and new players face key technical barriers such as the current energy storage capacity per unit weight of batteries—500 Wh/kg is widely regarded as the minimum required for electric flight with commercially acceptable payload-range characteristics—as well as light and efficient electrical generators, motors and power electronics able to convert, condition and switch to high voltage power.
On the regulatory side, airworthiness authorities will have to find approaches to certify novel aircraft architectures as for over fifty years commercial aircraft have not deviated from the gas turbine powered architecture. The Advisory Council for Aeronautics Research (ACARE) has brought about a united sense of purpose across the European aviation sector to shift towards greener solutions and has set challenging goals, such as achieving 75% CO2 emission reductions per passenger.
These challenges mean that we will probably witness a ‘More Electric-Hybrid’ commercially sized aircraft in the near future rather than an all-electric alternative. This could, however, still deliver real benefits through reduced emissions and allow for the development of motors and power electronics for the switch to fully electric operation in the far-reaching future.
Further reading
References
- https://ec.europa.eu/clima/policies/transport/aviation_en
- https://www.independent.co.uk/environment/climate-change/your-carbon-footprint-revealed-climate-change-report-finds-we-each-produce-11-tons-of-carbon-a-year-427664.html
- www.theicct.org/blogs/staff/overturning-conventional-wisdom-aircraft-efficiency-trends
- Current and emerging trends in the aerospace sector – Atkins
- https://www.slideshare.net/WSAtkins/electrification-of-aircraft-102581749
- https://press.siemens.com/global/en/feature/electric-flight
- https://www.pbs.org/wgbh/nova/article/morphing-wings/
Categories & Tags:
Leave a comment on this post:
You might also like…
A beginner’s guide to sourcing a company beta
Beta is the measurement of a company’s common stock price volatility relative to the market. If you’re trying to find a current beta for a company there are a number of places to look. These ...
Credibility, confidence and collaborative focus: The impact of studying for a sustainability apprenticeship at Cranfield
For participants on Cranfield’s Sustainability Business Specialist Apprenticeship, it doesn’t take long for their studies to start to have an impact, with that impact ranging from personal growth and career progression, to organisational effect ...
Meet Mendeley: a powerful referencing tool that does the hard work for you!
Are you looking for a way to manage your references, create in-text citations and reference lists for your assignments or thesis? If so, you may wish to consider using Mendeley. What is it? Mendeley is ...
Adding documents to your Mendeley account
To make the most of a Mendeley account, it is useful to create and maintain a ‘Library’ of references. You can add references and documents to this Library in a number of ways: 1) Drag ...
Choosing the right reference management tool for you…
Are you thinking about using reference management software to help you manage your references? The Library is here to help you. While Mendeley has been our go-to reference management software for some years, we've recently ...
Cranfield Seed Fund recipient, Cosysense, are using AI to solve air conditioning problems and provide a net zero alternative
If you’ve ever worked in an office environment you’ve probably been involved in, or overheard, a conversation about the air conditioning. Well, it’s no surprise it’s a common complaint when research shows that up ...
HI Jason
I sign books for American Institute of Aeronautics and Astronautics and am interested in doing a book on the current state of electric aircraft research, maybe as a collected volume.
You seem to be wired into this field, and I wonder of we could talk? Perhaps you could kindly send me your email…
Thanks
Robin Rees
European Publishing Consultant, AIAA