A sit down with Krzysztof Koziol
01/08/2019
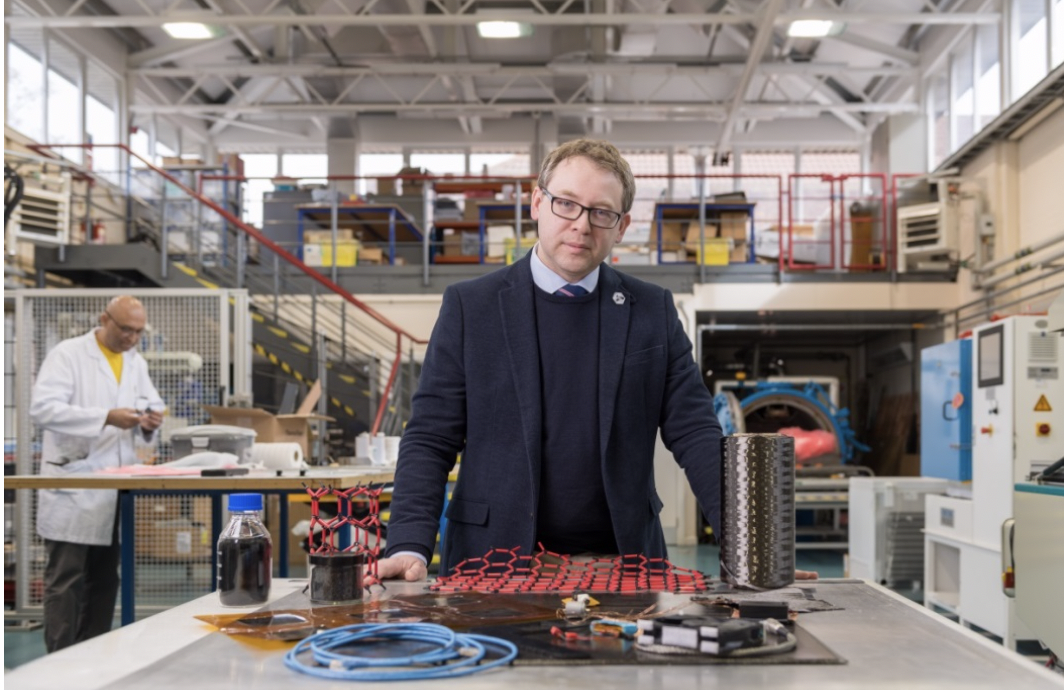
Improved efficiency and enhanced safety; breaking boundaries with new, sustainable composites
Why did you come to Cranfield?
“Cranfield is very well known, especially when you look at the applied science and technology. In my career path, I have developed materials and taken them into application, showing how they will turn into functional products. I found it very attractive when the position became available at Cranfield, I saw that I could really push forward some of the ideas that I had, and test them and translate them into the real world. That is what Cranfield does best.”
Give us an overview of the Enhanced Composites and Structures Centre
“The centre, historically, was very much focused on looking in to the development of aerospace composites, because we’ve always worked with companies such as Airbus, Safran, Boeing and Bombardier.
“The centre has since been engaging in new areas, such as the automotive industry as they have been seeking more lightweight structures. We have learned how to look into volume composite manufacturing at low cost, and also using recycled materials, embracing the new era of sustainability. We have been looking into the construction industry as well, and engaging with some partners that are looking into rapid housing development or use of sustainable materials, which will not only reduce the cost of the build, but also make the house more efficient.
“We have also been working with what I call the more ‘extreme environment’ industries like space and formula 1, which are really looking for new materials, pushing boundaries of materials because of performance and also because of safety, so there are also safety aspects which we have taken as a challenge and are trying to resolve.”
What are the biggest challenges when we think of manufacturing?
“From a materials perspective, industry is looking for materials that perform. The issue with this is the security of the supply of those materials. Companies need to make sure they are getting the same material over and over again. The other aspect to mention is sustainability. Industry is really actively now looking into materials that not only perform but ones that are also sustainable. It is a constant challenge for industry to find new, sustainable materials.
“On the manufacturing side, things are also changing. A lot of 3D printing approaches are being scaled up to something we have never seen before. I am talking about a large scale 3D printing of an aircraft wing by using a series of robots that will deposit materials and fibres, building up a high performing structure. We need to ensure we can manage this significant upscale.”
Tell us about some of the projects you are working on
“We are looking at completely new manufacturing directions which are not heard of or known to people at the moment.
“We have been pushing boundaries in the area of new generation conductors; this is specifically the area I work on in the centre. We are making carbon Nano-tubes and turning them into wires, the idea is to replace copper or aluminium conductors that are not necessarily performing that well, we also want to reduce the weight. To give you an idea, a Boeing 747 carries about 5 tonnes of copper as a conductor on board, and we think we can drop it to 0.5 tonnes, that means that there is the potential for 4.5 tonnes of something else being carried, at every take off and every landing.
“We are also working on one project that is taking us into a completely new dimension of 3D printing of gloves, specifically surgical gloves where you require the perfect fit for surgeons’ hands. We are looking at how to make these gloves that are custom fit within seconds, opening directions where we have not been before. This is what we do at Cranfield.
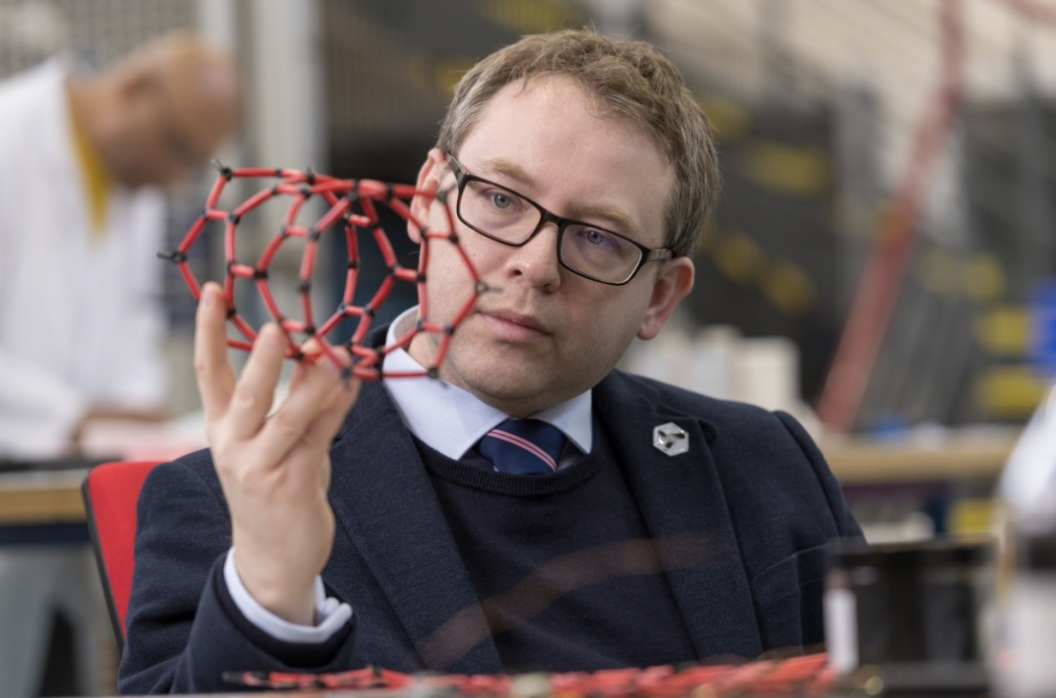
How does your centre support industry?
“We engage a lot with industry. I think the reason why industry come to us is because we understand what they want, which is very important, to know what the industrial partner is looking for and offer a programme that is on a reasonable timescale for development, but at the same time doing it with the accuracy of a thorough academic study. Bridging the expectations from our industrial partner to our academic rigor is what we do very well, Cranfield have been doing this for many years. We also have time, we have people who can dedicate their time on the problem, we don’t treat these projects as side projects, and we treat them as main projects as part of our job here.
“We are also very flexible on the funding of projects, with the ability to start small scale, or what we call a proof of concept, testing ideas. By doing this we are reducing the risk of industry having to heavily invest in specific idea. If the idea works, we can take it to mid or full scale.
“We have students who go through their MSc programme and then stay on with us in the centre, they like the work that we do. They might continue on a research career path, and some will then join our industrial partner. The industry is happy because they are getting very well trained individuals, who not only have a deep scientific knowledge, but an understanding of how knowledge needs to be applied, and how we can solve the real problems.”
Give us a unique experience you have had whilst working at Cranfield
“A unique experience I had here related to one of the group projects, where four to five students work on a project for around two months which I supervise. The projects allow students to really push boundaries and present new ideas. I had a group of four female student engineers who were working on a new concept which aimed at creating a ground to space drone. The idea was to make a drone which can travel all the way from the ground straight up to the international space station, almost acting like a communications platform between the earth and the international space station, without the use of expensive rockets.
“I was glad I had a team like this exploring something so challenging, It really opens up new concepts and visions which are completely out of this world, and also enables us to push materials to high extremes.”
Professor Krzysztof Koziol is a Professor of Composites Engineering and the Head of the Enhanced Composites and Structures Centre at Cranfield University. After graduating as a chemist, Professor Koziol did a PhD in materials science, and was awarded a Royal Society University research fellowship (URF) for his research and expertise in materials science.
Categories & Tags:
Leave a comment on this post:
You might also like…
Mastering the art of revising your writing
You’ve done the research and written your first draft. Now it’s time for one of the most crucial jobs as a writer - revising your writing to ensure your reader does not have to work ...
A ‘hands-on’ take on warehouse design as part of my Logistics and Supply Chain MSc
As part of my core module for my Logistics and Supply Chain Management MSc, I had the amazing opportunity to work on a warehouse design project a few weeks ago. The problem statement for ...
Thinking about your literature review?
As part of your PhD or Master’s thesis, you will probably have to write a literature review. A successful literature review will offer an analysis of the existing research in your field, demonstrating your understanding ...
A beginner’s guide to sourcing a company beta
Beta is the measurement of a company’s common stock price volatility relative to the market. If you’re trying to find a current beta for a company there are a number of places to look. These ...
Credibility, confidence and collaborative focus: The impact of studying for a sustainability apprenticeship at Cranfield
For participants on Cranfield’s Sustainability Business Specialist Apprenticeship, it doesn’t take long for their studies to start to have an impact, with that impact ranging from personal growth and career progression, to organisational effect ...
Meet Mendeley: a powerful referencing tool that does the hard work for you!
Are you looking for a way to manage your references, create in-text citations and reference lists for your assignments or thesis? If so, you may wish to consider using Mendeley. What is it? Mendeley is ...