Lufthansa Technik – Malta Study Tour 2019
02/05/2019
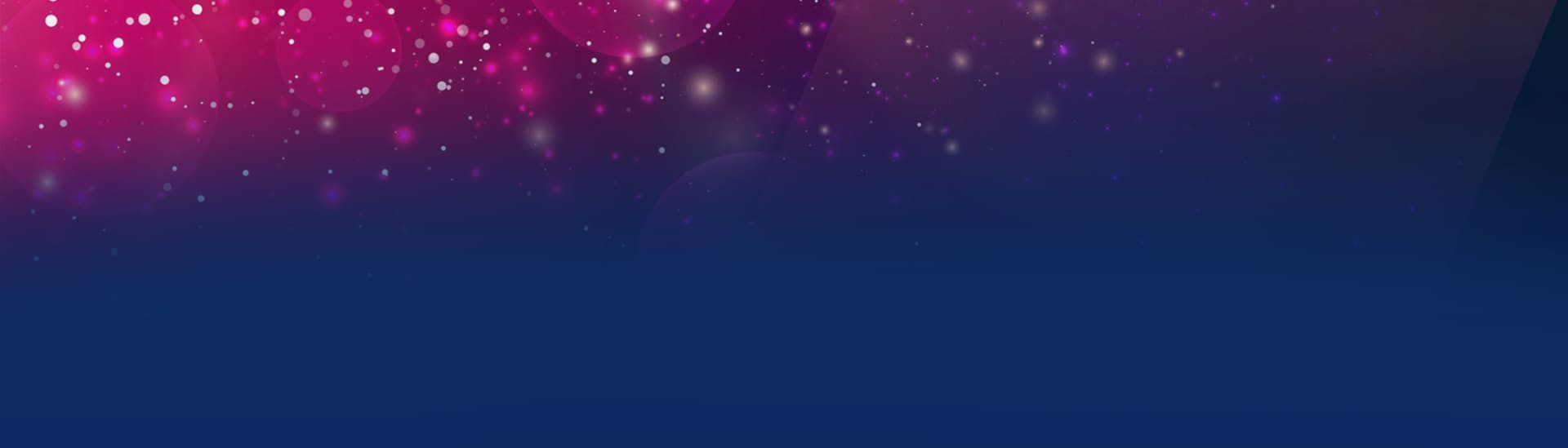
During the study tour in Malta, we had the chance to visit Lufthansa Technik. It is a maintenance centre where they check and repair aeroplanes from different airline companies including Lufthansa.
The production part of the site has a capacity of 7 aircrafts and offers mostly C-checks (every 12 to 18 months) and D-checks (every 4-5 years). Aircraft maintenance checks are periodic inspections that have to be done on all Airlines and other commercial operators of large or turbine-powered aircraft. A and B checks are lighter checks, while C and D are considered heavier checks. As the product is extremely expensive and valuable, every action made on the plane must be listed and comply with the customer demand. When a new issue has been revealed, they have to first wait for the airline company to agree for them to change or repair that part. As there is an exhaustive list of things to check, they implemented a very clear visual management system to keep track of the work progress. It is very important to remain on schedule or be able to predict exactly how much delay there is going to be, if there is a delay, as the planes are used for commercial flights. This management system also enables the presentation of KPIs such as productivity and number of working hours. With colour-coding it is easily understandable if the team did well, or not, each day.
As there is an incredible number of parts on each plane and which varies according to the plane type and the airline company, an optimised warehouse is a key factor in the success of the company. There are on average 800 parts each day which are being sent from the warehouse to the production lines. The receiving process takes time as different inspections are required to check all the parts received. In fact, the team explained “Swiss cheese” effect to us: the different checking will enable to find the different hole of the cheese. As their expertise is different, they do not see all the same holes.
One thing which did amaze us is that the warehouse deliver the spare parts to the hangars required with a bicycle, this is a really good eco-friendly initiative. Picking is manual and parts are either brought to the hangars, despatched to other Lufthansa Technik facilities or given back to the different airlines when required. In addition, 3D printers are used in Lufthansa Technik, they enable the staff to print some specific spare parts they need.
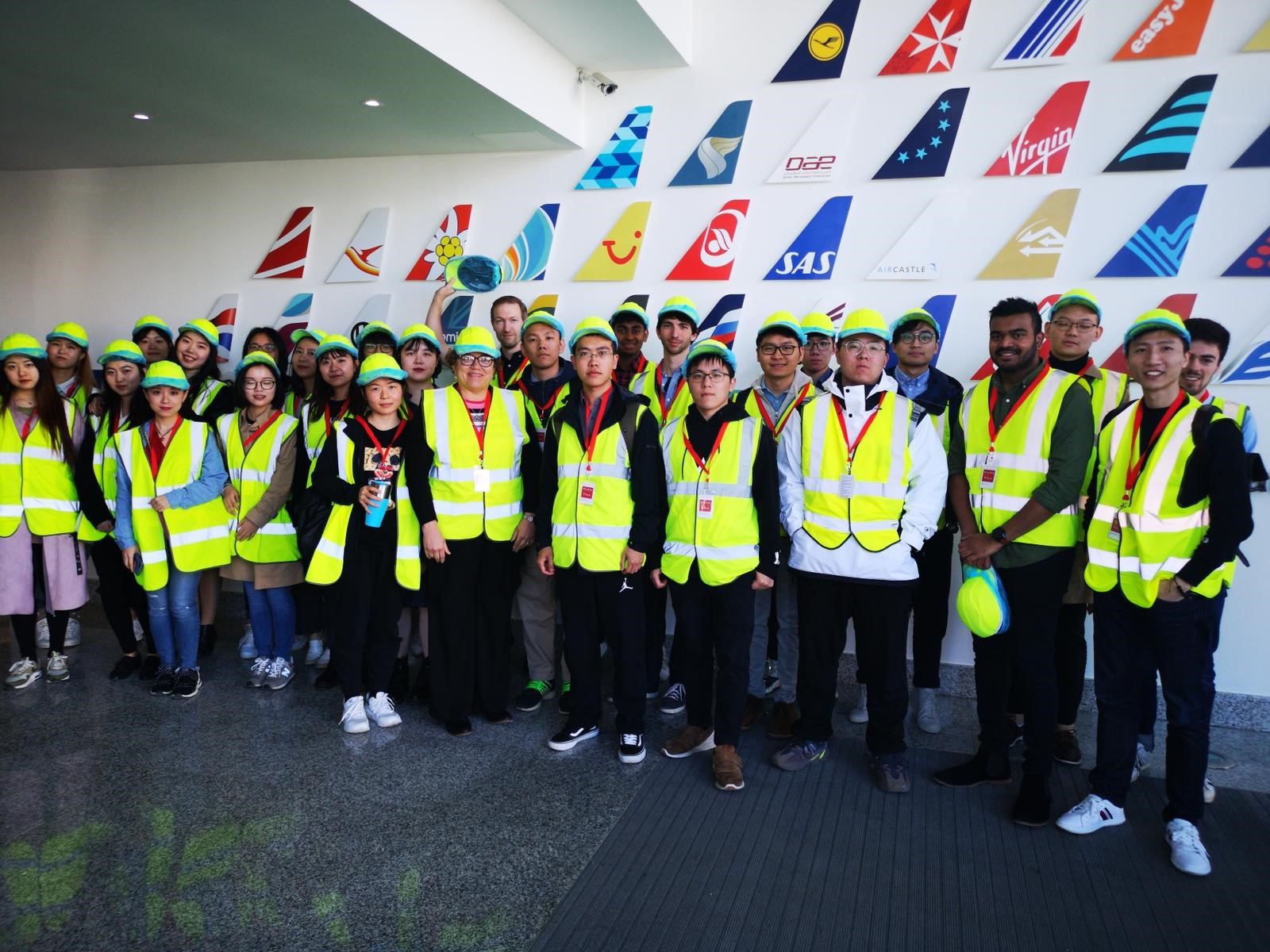
A big thanks to the people that contributed to the organisation of this visit. It was really interesting and impressive to see how in practice concepts are applied to this specific sector.
Categories & Tags:
Leave a comment on this post:
You might also like…
From taxidermy to forensic investigation: My journey at Cranfield
Christina Recheis completed her MSc in Forensic Investigation at Cranfield University in 2021 and specialised in forensic archaeology and anthropology. Her master's thesis focused on developing an algorithm to facilitate the identification of human remains, ...
Country stability and risk in BMI Research
If you need to know about country stability and risk, there are two Library services you ought to be looking at BMI Research. Country Risk report in BMI Research BMI covers country ...
How to present well as a group
You will have put a lot of work into your research or project and want to show everyone what you have achieved or discovered, so you need to impart this knowledge as clearly as possible. ...
Exploring the skies and beyond: My experience as a GREAT Scholar at Cranfield University
A place where innovation meets practice Cranfield University is renowned for its world-class facilities and resources. What stands out most to me though, is its unique connection to the aerospace industry. ...
Creating a new user account in Mendeley
Before you start using Mendeley reference management software, you will need to create an account. This is a really simple process and should take you no more than a couple of minutes. Just follow the ...
Shifting Gears: How virtual prototyping is driving the future of automotive and motorsport
The roar of the engine, the thrill of the track, the relentless pursuit of perfection – these are the hallmarks of racing cars. But even in the world of high-octane performance, ...