A closer look into the warehouse of a high street fashion brand
28/02/2020
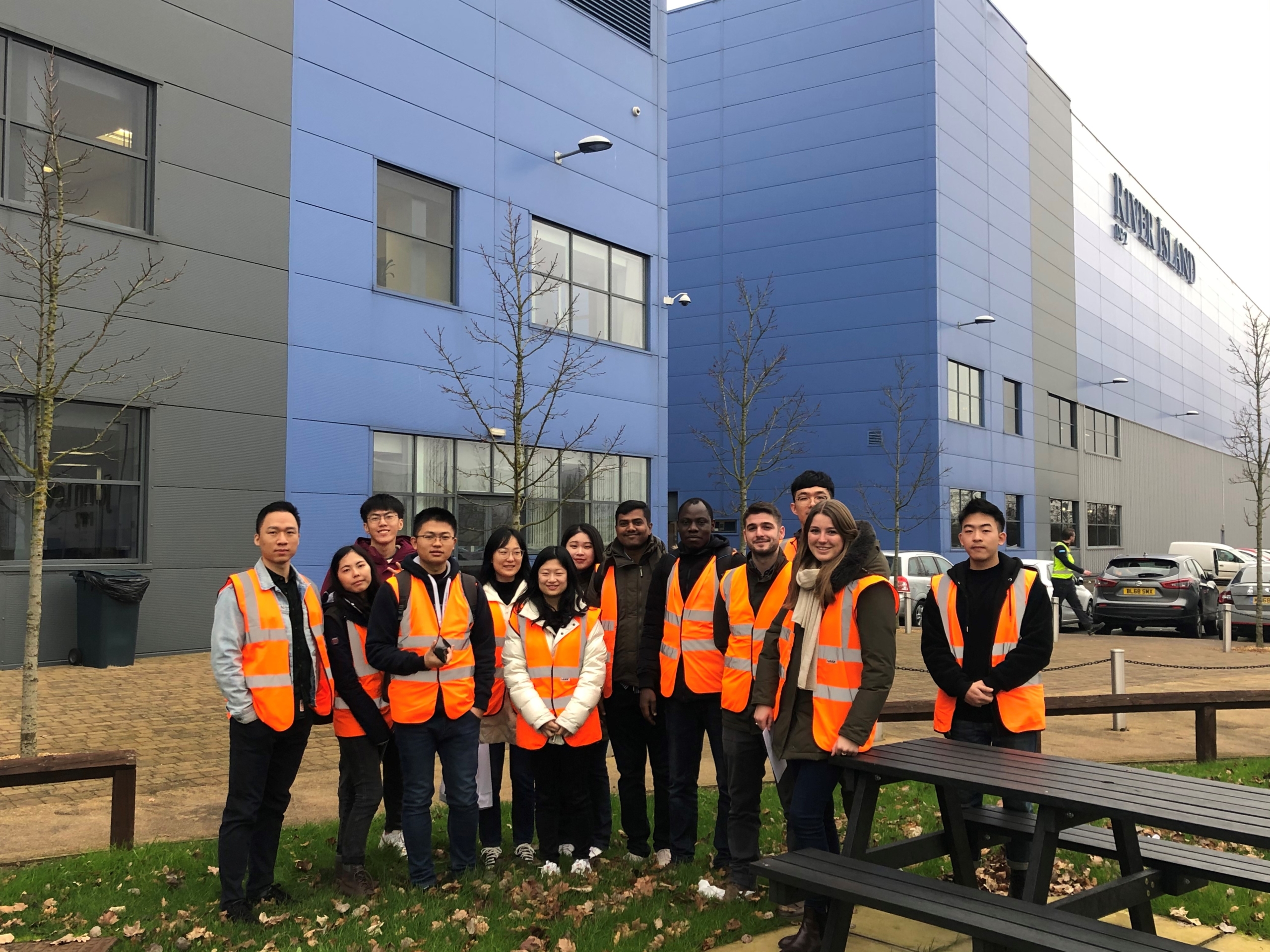
As part of our second term of the Logistics and Supply Chain MSc we got the opportunity to join a warehouse visit. In my case we went to the River Island distribution centre (DC). Luckily Cranfield School of Management benefits from being in the middle of a logistically important area in the UK. Hence there are plenty of newly established warehouses around the area of Milton Keynes due to its strategic location close to London.
Even though for me this was not the first chance to have a closer look at warehouse operations, it was still an exciting visit especially regarding the fashion supply chain specific processes that we saw. River Island operates only this one warehouse worldwide which requires the warehouse to serve all the different sales channels, such as online retailing, wholesalers and deliveries to own stores across Europe as well as distribution to international stores. Thus, River Island has developed their products in a so-called “Omni product” manner to create a “one-fits-all (distribution channel)” product.
We were able to get a tour through the 90,000 m2 warehouse which is split into two purpose build warehouses covering all processes from “goods in” until the outbound processes where lorries are loaded with the respective orders bringing fashion to its final customer. For their top 50 stores across the UK, River Island ensures a 24-48 hrs time frame from the moment the cartons enter the warehouse until they are received by the dedicated store.
On a regular day, the warehouse handles around 10,000 incoming cartons which can increase up to 15,000 – 16,000 cartons during peak times. However, no matter how much is received, the company puts its highest priority on the accuracy and quality of the received goods. There are multiple spot checks done based on the company’s accuracy standards also considering for instance the accuracy ranking of the different suppliers that produce the men’s, women’s and kids wear as well as a wide range of shoes and accessories. The credo that is followed here refers to keeping any errors and the number of items with insufficient quality as low as possible from the beginning to have the highest quality output when products are leaving the warehouse.
Besides their accuracy it was also interesting to see that one part of their warehouse is solely dedicated to storing up to 1,500,000 meters of fabrics that are used to produce hanging garments around Europe. This is very unique in the fashion industry where warehouses usually store ready to sell clothing items instead of raw fabric that is delivered to production facilities. Overall the hanging garments were one of the most exciting part for me as they are stored and transported in an entirely different way through the warehouse. In one part of the warehouse there is a railing structure installed at the ceiling where the hangers are connected to. In this way, the products are stored and moved throughout the warehouse until they end up at the outbound loading docks. The hanging clothes are literally flying down from the first mezzanine floor to the ground floor for loading, which was exciting to see.
Lastly, I was especially impressed by the experience of the team that was guiding us. Two of the senior managers took the time to give us a detailed tour covering as many of our questions as possible. Both senior managers combined had more than 44 years of River Island experience and they had both started their careers on the shop floor. The broad knowledge covering both operational and more strategical topics was remarkable.
Thanks again to Cranfield School of Management for making this warehouse visit happen and for allowing everyone to get a better feeling for what is actually happening on the shop floor and adding some practical examples in addition to our regular lecture material.
Categories & Tags:
Leave a comment on this post:
You might also like…
Creating a bibliography is easy in Mendeley
If you’re using Mendeley Cite, Mendeley's citation plug-in for Word, you will soon be ready to generate a bibliography of all the references you have cited. Here we’ll run through how quick and easy it ...
Why it pays for companies to free female employees from the baby trap
This is an extract from an article originally published in Ethical Corporation magazine. Read the full article. There is growing representation of women on company boards in the UK, with women making up 43.4% ...
Working on your poster presentation?
Are you going to be delivering a poster presentation here at Cranfield in the next few weeks? Looking for guidance to help you make it effective and successful? The format is a unique and wonderful ...
From Cranfield to Coca-Cola: Khushbu Tolani’s inspiring Management MSc internship journey
Hello, I am Khushbu Tolani, a passionate and ambitious individual who recently achieved a significant milestone during my time studying at Cranfield University. I was the first in my family to study abroad and ...
Introducing… W – Bloomberg’s Security Worksheet function
Bloomberg users, are you fed up hitting download limits? Do you want to create custom templates that download only the data you want and nothing else? Using many of Bloomberg's download templates often leads to ...
Managing your research data – a progress update
As you will already be aware, in 2024 we undertook a major, multi-phased project to redevelop our University research information system (CRIS), our institutional repository (CERES) and our research data management software (CORD). The ultimate ...