World’s first composite recycled racing kayak takes to the water for 125 mile race
13/04/2017
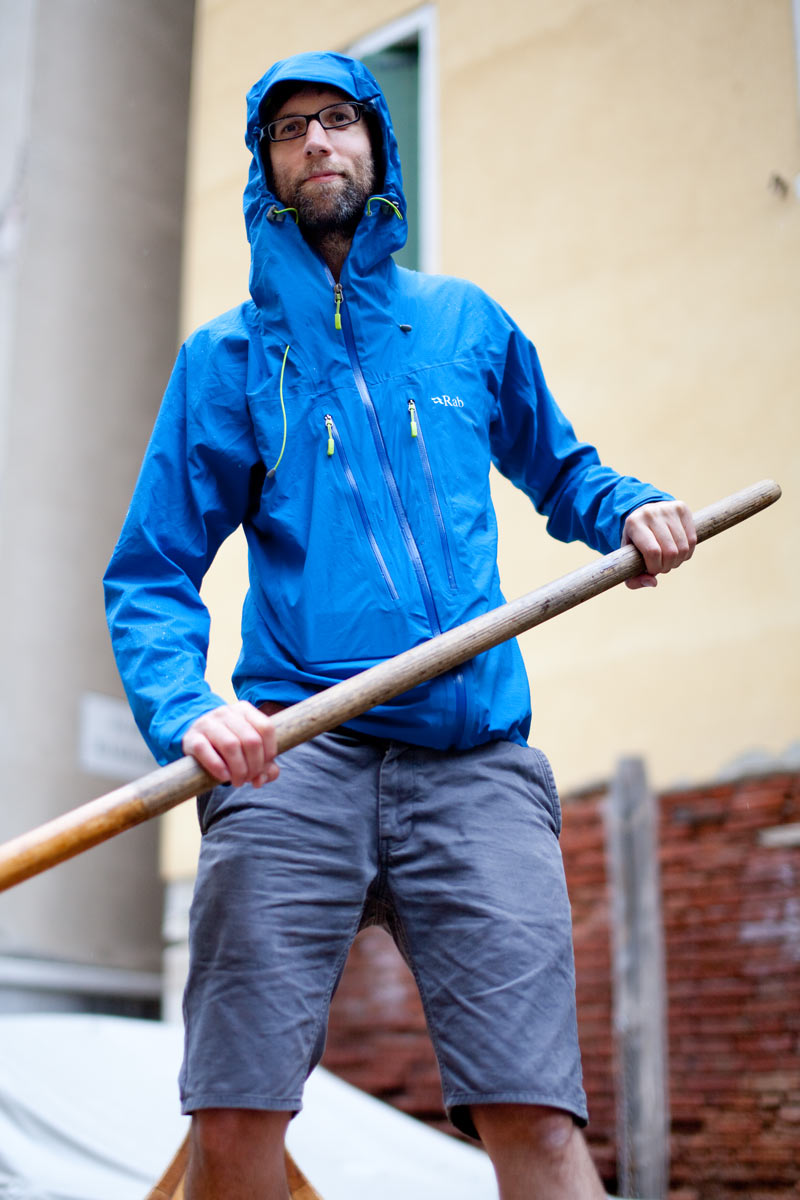
Kirton Kayaks have manufactured lightweight composite racing kayaks and sea kayaks for the past 50 years. Being the largest racing kayak manufacturer in the UK – K1s and K2s – their goal to progress and be the best manufacturer they can be meant they were the obvious choice for Professor Gary Leeke to work with to produce the first composite recycled racing kayak as part of his research into recycling fibre-reinforced composite waste.
Ahead of the kayak’s run in the Devizes to Westminster race this weekend, we interviewed Kirton’s Ben Turner about the project…
The challenge
“World resources are diminishing and we need to be aware of that. In the composites industry, it’s evident that we’re very reliant on carbon materials. Carbon has a huge carbon footprint, as does glass fibre, and all the major resins are from a petrochemical source. So moving to cork for the core material, using a waste product from someone else’s manufacturing process that they can’t use, and using resins with part biomass material – those are all steps in the right direction.
The proof
“The Devizes to Westminster International Canoe race (DW) is a fantastic test bed for any new design and innovation. It’s a huge race – 125 miles – straight through in one go. It normally takes paddlers 18-24 hours to complete it and it’s a huge feat of what the body can withstand. And if a new product can get to the end and remain in one piece, you know you’re onto something that worked. I would say there are no other races in this country that put a boat through the same level of pressure as the that race. Particularly when people are tired, the boats are really knocked around. So if it can make it through the DW, it shows that Gary got his composites right as far as boat building is concerned, and we were able to put it together right – so it’s the perfect test bed for us.
“If a product like this was available for the right price, we would certainly be looking to take it up with our top-end boats. Just on the moral grounds alone, it’s something that every manufacturer needs to be doing.
How it got started
“Gary approached me; this was quite some time before we started the project. He was looking at working with some recycled materials and asked us if we’d be interested in working with him. To which we said yes, not really knowing what would be involved at that time.
“He approached me with a recycled carbon material and his idea to make a boat out of it. It was quite clear Gary knew a lot of the chemistry and academic side of how to recycle the carbon composite and our expertise came in on how we can actually use it.
Challenges along the way
“The recycled material was quite a challenge, it’s not like a virgin piece of material, and it doesn’t have the same feel. The boats are made by hand and we’ve got skilled guys out there who are putting the laminates together and they had to learn how to handle the new material.
“We drove the direction of how we were going to use it, and found the right production methods to get it into a boat. We used a resin infusion process and modified the laminate a little bit to make sure the boat came within a manageable weight, because it was quite a heavy duty carbon that he’d sourced. We were able to use a partially recycled epoxy resin, so the epoxy was over 50% from renewable biomass sources. Finally, because making a solid carbon boat isn’t viable or practical if you’re doing the Devizes to Westminster race, in order to give it some stiffness and to keep the weight down, we also used a renewable cork material, which is specifically designed to work with composites, to try and keep the carbon footprint as small as we could.
“Gary knew a bit about racing boats and that was good because he understands the challenges and he turned it into a more exciting project. Working with someone within our sphere rather than just doing an academic exercise produced a shared outcome that we could both enjoy. The best bit is getting the boat finished, all the stickers on and seeing it ready to be paddled.”
Keep an eye open on @CranfieldUni on Twitter and Instagram for pictures of Gary & crew this weekend.
Find out more about the project in our case study.
Categories & Tags:
Leave a comment on this post:
You might also like…
Mastering the art of revising your writing
You’ve done the research and written your first draft. Now it’s time for one of the most crucial jobs as a writer - revising your writing to ensure your reader does not have to work ...
A ‘hands-on’ take on warehouse design as part of my Logistics and Supply Chain MSc
As part of my core module for my Logistics and Supply Chain Management MSc, I had the amazing opportunity to work on a warehouse design project a few weeks ago. The problem statement for ...
Thinking about your literature review?
As part of your PhD or Master’s thesis, you will probably have to write a literature review. A successful literature review will offer an analysis of the existing research in your field, demonstrating your understanding ...
A beginner’s guide to sourcing a company beta
Beta is the measurement of a company’s common stock price volatility relative to the market. If you’re trying to find a current beta for a company there are a number of places to look. These ...
Credibility, confidence and collaborative focus: The impact of studying for a sustainability apprenticeship at Cranfield
For participants on Cranfield’s Sustainability Business Specialist Apprenticeship, it doesn’t take long for their studies to start to have an impact, with that impact ranging from personal growth and career progression, to organisational effect ...
Meet Mendeley: a powerful referencing tool that does the hard work for you!
Are you looking for a way to manage your references, create in-text citations and reference lists for your assignments or thesis? If so, you may wish to consider using Mendeley. What is it? Mendeley is ...