How do structural engineers make sure an aircraft wing can carry the weight of the entire plane? Modelling failure of metals and composites
06/09/2017
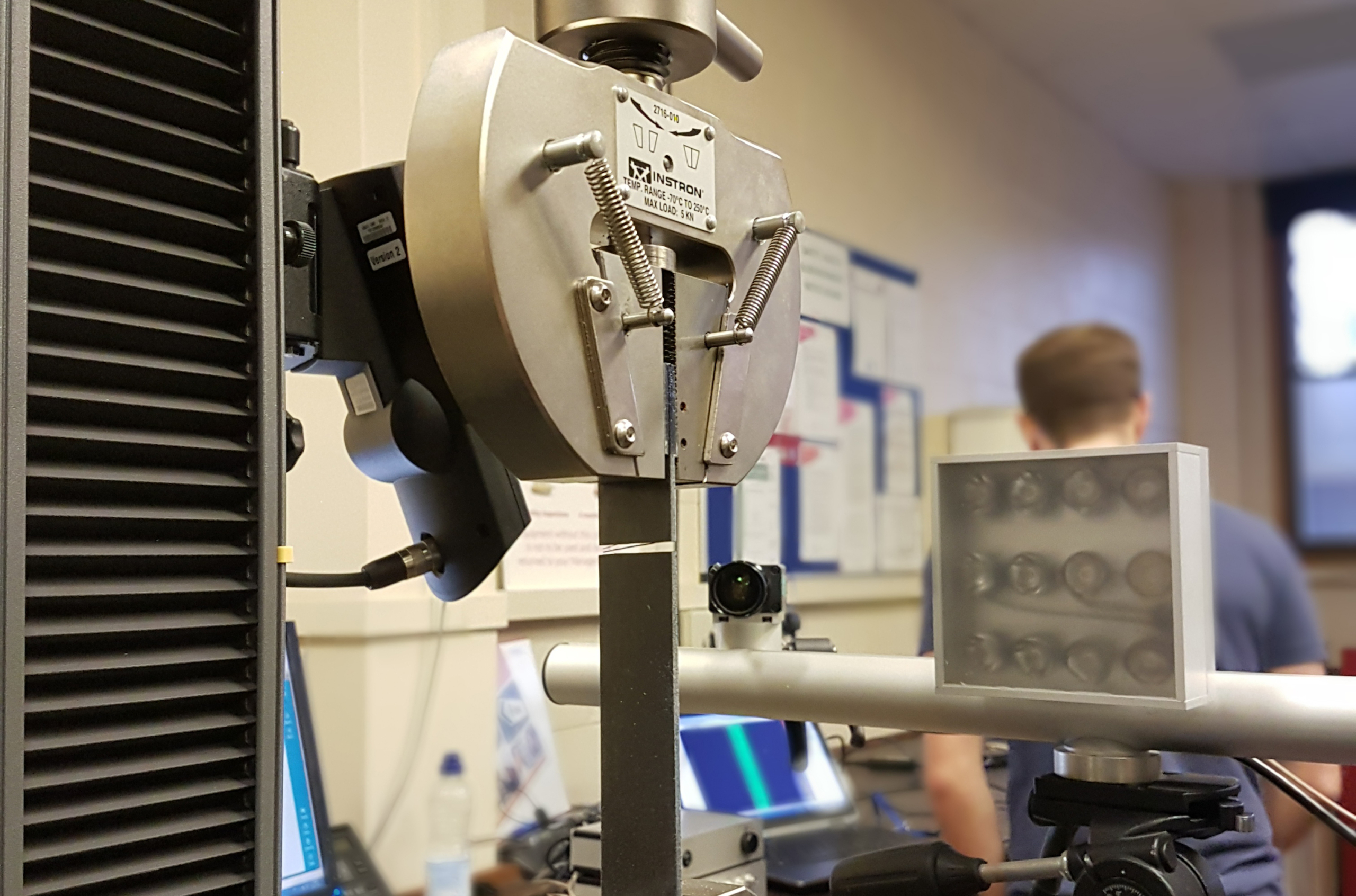
Being able to predict the behaviour of materials is one of the key skills of a structural engineer. A structural engineer must know how to design components so that they can carry the loads in service. An aircraft wing must carry the entire weight of the aircraft. The blade of the wind turbine must be able to carry the rotational inertia due to its spinning mass. These structures are designed with the full knowledge of the materials’ stiffness and strength. In some situations, a structural engineer wants to predict the behaviour of a structure once certain areas have failed. For example, when a vehicle crashes, the front part of the car must be designed to crush or crumble so as to absorb the majority of the impact energy. By predicting these behaviours accurately, structures can be designed to be safer and lighter, with less cost involved in the design and development process.
Numerical models such as Finite Element (FE) Analysis have become an invaluable tool used by structural engineers to analyse complex structural behaviours. Typically used to analyse stresses in a structure, advanced models have been created to allow prediction of failure as well. The challenge with these advance models is the uncertainty with the results. Relative to metallic materials, the behaviour of a fibre reinforced polymer composite material can be quite complex. The orthotropic nature of the material means much more information about its properties is needed.
For metals, you can pretty much define the bulk properties with two material constants: its modulus and Poisson’s ratio. Whereas to correctly define the properties of only a single layer of a composite material, as many as nine different material constants will need to be measured.
To model the failure process in metals (Figure 1), the full plasticity profile and the relationship of the local stresses and strains will need to be known. The ratio of tensile to shear stresses can have large influence on the failure strength of metal material and as such need to be considered in detail.
Figure 1 FE simulation of an aluminium open hole tension
Composites do have one advantage in the context of modelling failure. They are not ductile. Well, not to the same extent as metals. This means the behaviour of the material can be assumed to be brittle until failure, significantly simplifying the failure models. The advantages end there. A single composite ply will have different strength properties when tested in tension, compression and shear, whether in the direction of the fibres or transverse to it. How these strength properties interact, will determine the failure profile of the composite material. Even a simple tensile test on a laminated composite can produce very complex failure profiles, as shown in Figure 2 below.
Figure 2 Open-hole tension of an FRP Composite tensile failure [Source: AZO Materials]
The modules that I teach as part of our Advanced Lightweight Structures and Impact MSc cover the failure modelling of both metal and composites. I really enjoy seeing how students gain appreciation of the theory behind these techniques, how the material data is captured and important features of the model setup to look out for, which can have important influences on the results e.g. mesh dependence of failure growth (as shown in Figure 3 below).
Figure 3: FE simulation of open hole tension of FRP composite ply with fibres in 45° direction showing the mesh influence on the failure profile
Failure modelling of materials is not a closed question, certainly not for composites. Every year, we learn a great deal in the physical behaviour of these complex materials which allows researchers to create ever more accurate and efficient predictive models. Until virtual testing becomes the norm in structural design process, there is room to improve.
—
AZO Materials – Available at: http://www.azom.com/article.aspx?ArticleID=12335 (Accessed 29 June 2017).
Categories & Tags:
Leave a comment on this post:
You might also like…
Mastering the art of revising your writing
You’ve done the research and written your first draft. Now it’s time for one of the most crucial jobs as a writer - revising your writing to ensure your reader does not have to work ...
A ‘hands-on’ take on warehouse design as part of my Logistics and Supply Chain MSc
As part of my core module for my Logistics and Supply Chain Management MSc, I had the amazing opportunity to work on a warehouse design project a few weeks ago. The problem statement for ...
Thinking about your literature review?
As part of your PhD or Master’s thesis, you will probably have to write a literature review. A successful literature review will offer an analysis of the existing research in your field, demonstrating your understanding ...
A beginner’s guide to sourcing a company beta
Beta is the measurement of a company’s common stock price volatility relative to the market. If you’re trying to find a current beta for a company there are a number of places to look. These ...
Credibility, confidence and collaborative focus: The impact of studying for a sustainability apprenticeship at Cranfield
For participants on Cranfield’s Sustainability Business Specialist Apprenticeship, it doesn’t take long for their studies to start to have an impact, with that impact ranging from personal growth and career progression, to organisational effect ...
Meet Mendeley: a powerful referencing tool that does the hard work for you!
Are you looking for a way to manage your references, create in-text citations and reference lists for your assignments or thesis? If so, you may wish to consider using Mendeley. What is it? Mendeley is ...